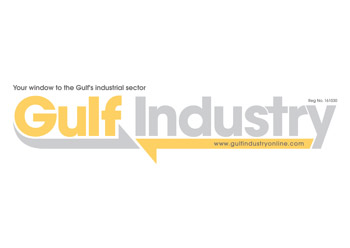
International oilfield service company Expro has announced the successful qualification and field trial of its FlowCAT retrofit wireless safety valve. The valve has recently completed a six-month trial in a gas well located onshore Southern Italy.
This success marks the first use of Expro’s award-winning Cableless Telemetry System (CaTS) in a flow control application.
CaTS is a revolutionary development in the field of reservoir monitoring and control, allowing information to be transmitted in real time to and from downhole instruments without the use of cables. Its two-way transmission capability enables the remote control of downhole instrumentation, opening the path to the radical redesign of downhole completions.
FlowCAT is a fail safe closed safety valve that can be installed in the well’s existing safety valve nipple profile, or by using an alternative suspension mechanism, and is controlled from surface using the CaTS Electromagnetic (EM) wireless telemetry technology.
Installed in December 2008, the 4.5-inch FlowCAT valve was deployed into the well using standard slickline intervention methods and, over the course of the six months, was cycled and inflow tested regularly during periods of both production and injection. The valve was seen to perform reliably and consistently throughout the test with no false closure events observed.
Steve Hudson, Expro’s wireless well solutions technology manager, said: “Now that we have proven the reliability of the valve mechanical components and the robustness of the wireless telemetry scheme over an extended duration test in the onshore environment, we are working to finalise the necessary system enhancements to allow us to take FlowCAT to the offshore platform environment. We feel well placed to take FlowCAT to offshore trial in the next three to six months.”
Milestone achievement
Brian Champion, general manager of Expro’s wireless business unit, said: “Our focus is now on the further development and integration of additional flow control, monitoring and wireless telemetry components to enable the retrofit of instrumentation into complex well architectures, including multi-lateral wells.”
The FlowCAT technology
The FlowCAT valve mechanism, which was developed for Expro by Petrowell Ltd, is of a poppet-type design. The valve is held open by the continuous transmission of EM signals from surface. If the signal transmission is interrupted or a “close” command is transmitted, then a spring will power the poppet into the closed position.
To re-open the valve and return the well back to production, an overpressure is applied from surface, the EM signal transmission is activated again to hold the valve open and then the overpressure is bled off. By interfacing the CaTS topside transmitter unit with the wellsite Emergency Shutdown System (ESD), it is ensured that control of the FlowCAT is integrated into the wellsite master safety control systems.
In situations where a surface controlled subsurface safety valve is rendered inoperable through plugging or damage to the hydraulic control line, the FlowCAT can be installed into the well on slickline and the well returned to production. The ability to control the FlowCAT valve wirelessly from surface without requiring cables or hydraulic control lines, offers both functional and safety benefits compared with alternative remedial solutions that may use subsurface controlled valves, such as storm chokes or velocity valves that operate based on pressure differential changes.