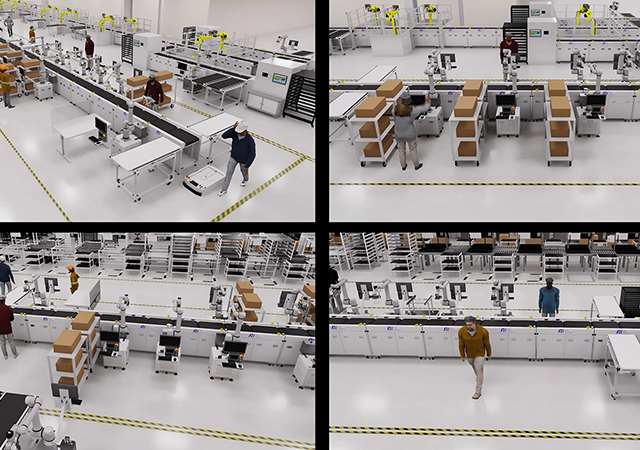
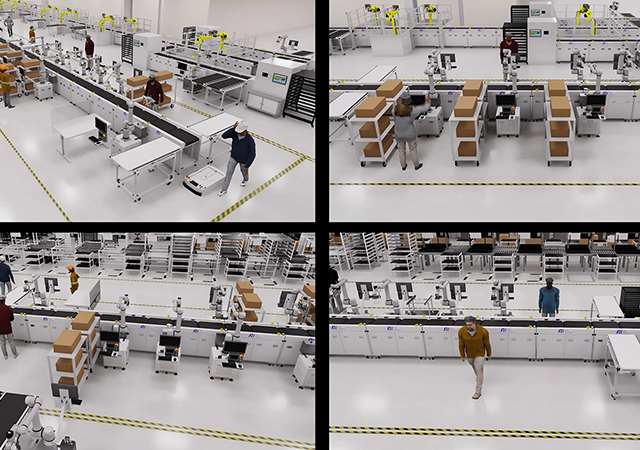
Improving manufacturing sustainability involves optimising all stages of the product lifecycle-from material sourcing and transportation to design, production, distribution, and end-of-life disposal, according to insight from NVIDIA, a leader in graphics processing units (GPUs) and artificial intelligence (AI) hardware and software.
The International Energy Agency estimates that a mere 1% reduction in the carbon footprint of industrial production could lead to an annual savings of 90 million tons of CO₂ emissions, which is akin to removing over 20 million gasoline-powered cars from the roads each year.
Technologies like digital twins and accelerated computing are enabling manufacturers to lower emissions, boost energy efficiency, and respond to the increasing demand for environmentally responsible production.
Siemens and NVIDIA are leading innovations that assist customers in achieving sustainability goals while enhancing production processes, according to NVIDIA.
KEY CHALLENGES IN SUSTAINABLE MANUFACTURING
Manufacturers often struggle to balance sustainability with profitability. A 2022 Ernst & Young study found that digital twins can reduce construction costs by up to 35%, highlighting the direct relationship between resource consumption and expenses.
However, a significant obstacle to sustainable manufacturing is the existence of silos within organisations-between departments, across different plants, and among production teams. These silos can result from conflicting priorities, a lack of unified energy-efficiency metrics, and the need for new skills and solutions to bridge these gaps.
Data management also poses a challenge, as many manufacturers find it difficult to convert vast amounts of data into actionable insights that support sustainability initiatives. A case study from The Manufacturer revealed that 25% of respondents acknowledged their data limitations hinder energy efficiency and environmental sustainability, with nearly a third reporting that their data is restricted to localised use cases.
To overcome these challenges, innovative solutions are necessary to dismantle barriers and leverage data for sustainability. Digital twin technology has emerged as a vital tool in this endeavor, acting as a central hub for information.
THE ROLE OF DIGITAL TWINS IN SUSTAINABLE MANUFACTURING
Industrial-scale digital twins, powered by the NVIDIA Omniverse platform and Universal Scene Description (OpenUSD), are transforming manufacturers’ approaches to sustainability and scalability. These technologies create digital twins that contextualise engineering data from multiple sources as it would appear in the real world, breaking down information silos and providing a comprehensive view accessible to all teams-from engineering to sales and marketing.
This enhanced visibility allows engineers and designers to simulate and optimise product designs, facility layouts, energy consumption, and manufacturing processes before physical production. As a result, stakeholders can make informed decisions that improve efficiency and minimise costly errors and last-minute adjustments, which can lead to significant waste.
Siemens is integrating NVIDIA Omniverse Cloud APIs into its Siemens Xcelerator platform, beginning with Teamcenter X, its cloud-based product lifecycle management software. This integration enables Siemens to harness photorealistic visualisation for complex engineering data and workflows, helping companies create physics-based digital twins that reduce workflow waste and errors.
Companies like HD Hyundai, a leader in sustainable ship manufacturing, are utilising these new capabilities to visualise and engage with intricate engineering data on an unprecedented scale.
Furthermore, physics-based digital twins are being employed to test and validate robotics and AI before their deployment in manufacturing settings. For instance, Foxconn, the world’s largest electronics manufacturer, has created a virtual plant that redefines industrial automation. This digital twin platform, built on Omniverse and NVIDIA Isaac, replicates a factory in Guadalajara, Mexico, allowing engineers to optimise processes and train robots for the efficient production of NVIDIA Blackwell systems.
By simulating the factory environment, engineers can determine optimal placements for heavy robotic arms, enhance movement efficiency, and strategically position thousands of sensors and cameras to monitor the entire production process. Foxconn’s chairman, Young Liu, emphasised that this digital twin approach will enhance automation and efficiency, leading to significant savings in time, cost, and energy, with expectations of over 30% annual reductions in energy consumption.
MAKING EVERY WATT COUNT
As industries face rising AI demand, it is crucial for business leaders—particularly in manufacturing and data centers-to maximise energy efficiency and ensure effective utilisation of every watt to balance decarbonisation with AI growth.
Accelerated computing platforms that integrate GPUs and CPUs are vital for enhancing computational efficiency. GPUs, designed for complex calculations, can outperform traditional CPU-only systems in AI tasks, achieving up to 20 times more energy efficiency in AI inference and training.
This leap in efficiency has yielded substantial progress, enabling AI to tackle more complex challenges while maintaining energy-efficient operations. Businesses can further mitigate their environmental impact by adopting key energy management strategies, including energy demand management, scaling battery storage for short-duration outages, securing renewable energy sources, and exploring innovative solutions like heat reuse.
THE FUTURE OF SUSTAINABLE MANUFACTURING: INDUSTRIAL DIGITALISATION
The next stage in manufacturing is the convergence of the digital and physical realms, known as industrial digitalisation or the "industrial metaverse." In this context, digital twins will become more immersive and interactive, empowering manufacturers to make data-driven decisions more rapidly.
Roland Busch, president and CEO of Siemens AG, stated, “We will revolutionise how products and experiences are designed, manufactured, and serviced. This next generation of industrial software will enable customers to experience products in context and stunning realism, and in the future, interact with them through natural language input.”