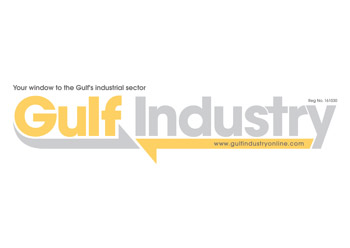

Quadrant CMS has won an order from Heineken Beer Systems to produce and package the polypropylene tap system for its draught keg – a portable and disposable system for serving quality draught beer.
The multi-part system is a critical, consumer-interfacing component on the new five-litre, single-use draught keg from Heineken.
Its production represents a first venture into the beverage market for Quadrant CMS while pursuing its strategy of developing and producing polymer-based parts for function-critical systems. With an internal volume of five litres, the Heineken keg is made of recyclable steel and involves a patented tapping technology that keeps the beer fresh in the refrigerator 30 days after initial tapping.
The easy-to-install tap system consists of five injection-moulded parts and a small extruded tube, all made of polypropylene, which is delivered in a blister packaging together with a protective plastic ring that doubles as a carrier-grip. All the components of the tap system are required to be robust and leak-free, withstanding the pressurised beer as well as fluctuations in temperature as the keg is moved in and out of refrigeration units.
The injection-moulded and extruded parts are produced and assembled at Quadrant CMS cleanroom production facilities in Tielt, Belgium, in compliance with Heineken’s quality standards. Moulded in a multi-cavity system due to the number of parts required, Quadrant CMS employs high-precision tools to maintain the high tolerance of the parts during serial production.