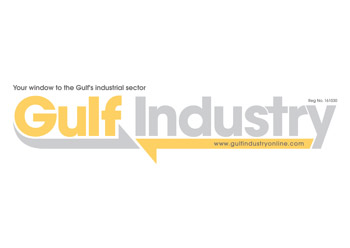

DSM Engineering Plastics has highlighted that its Stanyl polyamide 4,6 (PA46) is finding increasing use as replacement for metal in assemblies that have traditionally been made of metal and rubber.
“Designers gain new design freedom as well as reduced production costs by using Stanyl as the rigid component in such applications as automotive strut mounts, electromechanical anti-vibration and anti-shock mounts, energy-absorption compon-ents and exhaust hangers,” a company statement said.
“Replacement of metal with thermoplastics began decades ago,” said Paul Habets, application developments manager for Stanyl. “But, there are significant challenges when selecting the right material for applications with rubber components. Manufacturing req-uires high heat for vulcanisation, and many of the traditional rubber-to-metal components require very high stiffness and strength. In a rapidly growing number of applications, Stanyl meets or exceeds the mechanical and thermal performance needed for the rigid element in these products.”
Stanyl exhibits properties ideal for applications that marry a strong substrate to a relatively soft or compliant element: excellent creep resistance, high stiffness and strength, combined with heat resistance to withstand both vulcanisation and application environments, including automotive under-bonnet uses. The material can handle continuous use temperatures as high as 200 deg C with transient peaks of up to 250 deg C. Stanyl also provides good chemical resistance, particularly to grease, gasoline and oil.
Compared to metal, Stanyl is up to seven times lighter, and it is more easily formed into complex shapes. Compared to other engineering thermoplastics, Stanyl offers excellent weld line strength and fatigue resistance. It exhibits unmatched toughness and ductility compared to aluminium. Charpy impact values remain at a high level, even at temperatures below 0 deg C.
Stanyl offers potential cost reduction by eliminating production steps, including the grinding, degreasing, machining and other operations generally required for metal components. It provides excellent adhesion to rubber using conventional primers and adhesion systems. Finally, it offers both high wear resistance and compared to metals (even after surface treatment or polishing) a lower coefficient of friction.