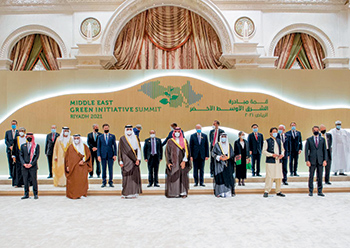
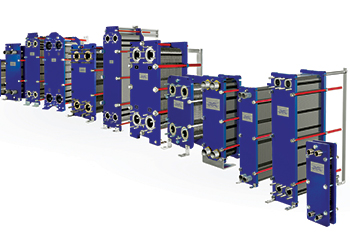
The decarbonisation challenge facing the world today is two-fold: we must simultaneously support rapidly growing energy demands, while reducing CO2 emissions to meet the goals of the Paris Climate Agreement. Achieving the Paris objective of limiting the global temperature increase to 1.5-degC by 2050 will require a “Sustainable Development” scenario. However, over the same period, energy needs are expected to grow by 54 per cent. No single, simple solution can transform the global energy system and global stakeholders across all sectors require a combination of technologies and fuels.
Energy efficiency is one of the main contributors enabling the successful achievement of the goals of the Paris Agreement. In fact, according to the International Energy Agency, improved energy efficiency could account for more than 40 per cent of emissions reductions in the next 20 years. As much as 50 per cent of today’s potential for energy savings comes from the industrial sector, and 30 per cent can be achieved through more energy efficient buildings. Encouragingly, the solutions to enable these energy efficiency improvements already exist.
Businesses are now adopting world-leading sustainable solutions to increase competiveness and reduce carbon emissions. The culmination of decades of investment in innovation, plate heat exchanger technologies help businesses optimize energy use in their processes. Gasketed plate heat exchangers make it possible to save dramatic amounts of energy and thereby reduce carbon emissions. Increased efficiency means not only benefits for the environment but also financial savings for the operator.
The primary risk to the energy efficiency of plate heat exchanger comes from suppliers’ undersized designs or application of sizing tolerances. Manufacturers are being compelled by competitive market constraints to size gasketed plate heat exchangers with negative tolerances. Accurate measurement of these tolerances is impossible with normal instrumentation due to seasonal and variable loads, and underperformance has a significant negative impact on the operating expenses of related machinery such as pumps and chillers. Therefore, a correctly sized gasketed plate heat exchanger can increase the operational efficiency of the whole process, and prevent any process disruptions that might occur under high load.
AHRI PERFORMANCE CERTIFICATION
There is one guaranteed way to certainty right from the start – AHRI Performance Certification. The Air-Conditioning, Heating and Refrigeration Institute (AHRI), a non-profit organization, is the only independent third-party organization that certifies the performance of plate heat exchangers globally.
Most importantly, AHRI Performance certification eliminates concern about calculations and promotes a stronger focus on energy efficiency, which will foster innovation and stimulate manufacturers to develop more efficient products. Consequently, gasketed plate heat exchangers designed and supplied with AHRI Performance Certification, ensure sustainability by default.
Alfa Laval has chosen to take an active role in promoting AHRI certification in the Middle East. From every perspective, AHRI certification is better for everyone involved in the process of designing, producing, selecting, and operating plate heat exchangers. Performance certification is an important step in creating a sound plate heat exchangers market and benefits the industry as a whole.
Alfa Laval for example was the first in the region to offer a broad range of heat exchanger innovations – the AlfaQ range – certified to AHRI 400 and boasting a 100 per cent success rate in the AHRI performance certification program for more than a decade.
GASKETED PLATE HEAT EXCHANGERS
Open cooling tower systems are also a source of increasing levels of calcium carbonate and corrosive chloride ions in the circulating cooling water. These unwanted minerals enter via make-up water and accumulate over time to unacceptable levels. The water in the open cooling tower water loop evaporates, but the minerals stay and increase in concentration in the cooling system.
Over a six-month period, calcium carbonate and chloride ions can double in concentration. The only way to clean the system of these unwanted minerals is to periodically flush the loop. This cleaning results in increased operational costs and is normally not done as water costs are high.
Increasing the concentration of calcium carbonate minerals in the cooling water loop will cause major losses in energy efficiency and higher pumping costs. Furthermore, the reduced diameter of cooling water pipes, maintenance, replacement of cooling equipment, and unexpected shutdowns will all mean losses in heat transfer efficiency, requiring more cooling water and thus further investments in cooling tower capacity.
In addition, the condenser is often the hottest point of the cooling tower loop. With condensing temperatures of 80-degC, it is here that most of the scale forms, and adheres to hot condenser surfaces. With a gasketed plate heat exchanger installed to protect the condenser, the formation of scale is reduced, as wall temperatures will be 30-40-degC. Scale CaCO3 behaves opposite to that of sugar. The higher the surface temperature, the greater the formation of scale on hot surfaces.
There are major benefits of a gasketed plate heat exchanger when used as interchanger:
• Savings in chiller running costs as a result of a condenser free from fouling and scale.
• Savings in pumping costs with clean pipes, as the diameter does not reduce due to the adhesion of calcium deposits on hot inner pipe surfaces.
• Savings in reduced maintenance costs of downstream cooling equipment such as shell-and-tube heat exchangers.
• Less money spent on chemical dosing and treatment of a smaller volume of open cooling tower loop. Typically, 10 per cent of overall cooling loop in volume.
• Fast simple and easy cleaning of gasketed plate heat exchangers by a single person in a few hours.
AHRI performance certification provides a third-party guarantee of 5 per cent of duty load in kW and 5 per cent of specified pressure drop. The latest trend of protecting the chiller condenser from the harmful effects of an open cooling tower will provide savings to owners and managers of cooling systems, to the level of an average 10 per cent per year in chiller electricity running costs.
In conclusion, efficient gasketed plate heat exchangers in the market will perform according to specification and ensure a lower life cycle cost for numerous other cooling equipment throughout the plan.