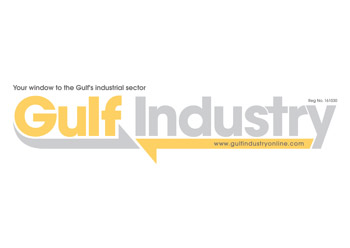

Riyadh-based Saudi Pump Factory (SPF) is all set to play a major role in a unique project in the Kingdom. United Lube Oil Company (Unilube), a SR200 million ($53 million) Saudi-British joint venture will build a 75,000 tonnes per year waste lubricants recycling plant in Jubail.
As part of the overall contract, SPF signed a pump supply contract with Unilube chairman Ali Al Jedaie, in the presence of British Minister of Trade Richard Caborn.
Unilube is expected to bring economic advantages to Saudi Arabia, as well as providing significant environmental benefits.
''The British government is very pleased that a major beneficiary of the Offset initiative should also result in such an important ecological boost,'' said Caborn.
The plant will, according to Al Jedaie, be the most modern recycling centre in the Middle East, using miniaturised refinery technology, and will be, in many ways, the most advanced plant of its kind in the world when it comes onstream before the end of this year. The plant will produce base lubricating oil at levels comparable to Luberef, Saudi Aramco's base lubricant refinery. Thus, customers will be assured of high quality products and improved supply streams at competitive prices.
For SPF, the Unilube contract is the latest prestigious deal won by the company. From its manufacturing base in Riyadh's Second Industrial City, SPF designs and produces high quality API ANSI, fire, API610 process and vertical turbine pumps.
Its state-of-the-art facility includes two- and four-axis CNC machining centres, and a computerised pump testing facility. A major factor in SPF's successes has been technical cooperation tie-ups with globally-renowned international companies such as Aurora Pump of the US and David Brown Union Pumps of the UK. These agreements enable SPF to widen the scope of its business opportunities.
The company's latest line of pumps, the ANSI series, is the product of SPF's centrifugal process/chemical pumping plant. The ANSI B73 Process & Chemical Pumps are designed for the erosive and corrosive liquids found in the process and chemical industries. Applications include non-API 610 process/chemical; process transfer and effluent and chemical transfer and effluent. The pumps are also used in the industrial process, paper and pulp sectors.
Through a policy of 'Providing Partnership' to its customers, SPF is at the cutting edge of valve and pump manufacturing technology for the oil, gas, petrochemical and industrial sectors.
ISO 9002-certified, SPF has forged strong, dependable relationships with highly respected contractors and consultants in Saudi Arabia, and is often specified by name as the recommended supplier.
Meanwhile SPF's introduction of a new line of ANSI pumps for tough applications was an innovative step.
The ANSI B73.1 Process & Chemical pumps are the product of SPF's centrifugal process/chemical pumping plant, and are designed for the erosive and corrosive liquids found in the process and chemical industry.
The heavy duty pumps, known as the ANSIPlus Series, have been developed using SPF's unrivalled experience and design and application know-how and expertise, and are now being used with success in a range of industrial applications.
Featuring heavy duty power frames and casing designs, maximum wear life (giving minimum downtime), high shaft and bearing strength, maximum bearing protection, a semi-open impeller design with pressure relief holes, rotodynamic sealing and available in a variety of material, gland sealing and baseplate options, the ANSIPlus range can generate up to 200 HP on 60Hz or 50Hz power supplies, have NEMA or European Standard Motors and offer full safety guards around all rotating parts.
In the chemical and petrochemical sectors, applications include non-API610 process/chemical; process transfer and effluent and chemical transfer and effluent. The pumps are also being used in the industrial process, paper and pulp sectors. The ANSIPlus range is the latest in a long line of high quality fire, API610 process and vertical turbine pumps designed and manufactured by SPF using state-of-the-art technology.
The SPF manufacturing facility on Riyadh's Second Industrial City includes two- and four-axis CNC machining centres, as well as a computerised pump testing facility, including NPSH. End suction and split case pump casings of up to 1.3 tonnes can be made.
Agreements with companies such as Aurora Pump and David Brown Union Pumps enable SPF not only to widen the scope of its business opportunities but also provide professional after sales support in Saudi Arabia. That and a stringent quality policy in force in the manufacturing process, SPF offers a complete service to its clients.
From Saudi Aramco to Sabic and a host of other satisfied clients throughout the Middle East, this ISO9002 certified manufacturer says that it can help reduce downtime thanks to the build quality and extensive range of products.
As it has formed strong, dependable relationships with highly respected contractors and consultants in Saudi Arabia, SPF is increasingly specified by name as the recommended supplier. The company remains the only pump manufacturer in the Kingdom to be approved by Saudi Aramco.