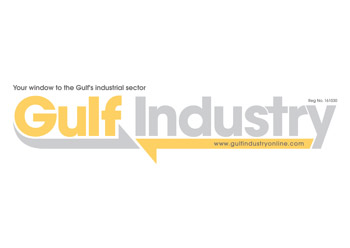
Saudi K-Span Factory for Steel Buildings has built up a reputation for an entirely different approach to pre-engineered building. Since starting operations in 1980, the company has reached an advanced level in terms of super-quality cladding, insulation and rapid installation and erection, implementing orders for hundreds of projects including buildings for the Saudi military, palaces, warehouses, factories, offices, markets and schools.
General manager Waddah Sabri, who is one of two shareholders of the company, the other being Dr Yousuf bin Abdullah al Saleem, says orders worth $75 million have been executed so far. Sales increased 30 per cent over the past year, and among recent clients has been the King Faisal Specialist Hospital. A feature of the Saudi K-Span factory, based in Riyadh's second industrial zone, is that it has all its components in mobile configuration, enabling its teams to go to the job site for fabrication and erection.
The company has entered into collaboration with Uskon, the only company in Turkey that has an ISO 9001 certification for its kind of operations. Uskon has also been awarded the TSE certificate for conforming to the requirements of the Turkish Standards Institute and is a member of the European Convention for Steel Structures. Saudi K-Span productions include insulated lightweight buildings for a variety of uses. The annual production capacity is 3,600 tonnes, which can be increased when needed. The products are from galvanised pre-painted steel whose quality competes for strength with concrete building.
"Our mobile factory can join your site with all the necessary materials needed for construction," says the company. "We have a well-trained team capable of erecting a building of 1,500 sq m in two days...The time consumed by others in designing we consume for constructing, thereby making our price very competitive when you consider the quality of our product."
The buildings erected by K-Span come into the broad categories of industrial buildings comprising factories, warehouses, garages, workshops and storages; agricultural storage facilities such as grain storage, space for fruit and vegetables, cold storages and storages with controlled atmosphere; oil industry structures encompassing any site facilities; construction sites such as stores and offices, and military buildings comprising aircraft shelters, tank shelters, maintenance facilities, dormitories and storage areas. K-Span also undertakes restorations including new roofs for old buildings. Projects executed by Saudi k-Span include the King Fahd Library, Riyadh; the Prince Faisal Bin Fahd Mosque, Al Shifa; the Kong Faisal Foundation, Riyadh, the Horseracing Court, Al Zulfi, the Capital Institute, Riyadh; the Bin Qassem Public Market, Al Khaima Park, gas stations at Madeni and Orabah Street, Riyadh; and military buildings including ammunition and hardware warehouses, hangars for the Royal Saudi Air Force and maintenance workshops for heavy vehicles.
K-Span's general features are that it uses straight or corrugated prepainted steel of 0.5mm, 0.7mm or 0.9mm. The steel structure being self-supported does not require a metal skeleton to carry it (ground-to-ground applications). The straight or arched individual panels are connected into a solid unit with an electric automatic panels seaming device. The TE R-120 generates 70 feet of permanent seam each minute without nuts, bolts or sealants of any kind while also being rust-free. The system is fire resistant and as solid as steel; lightweight enabling it to be disassembled and reassembled and has a wind load of 200 miles per hour; is flexible in formation according to the required design and fast in production and installation, the approximate capacity being 1,500 sq m per day.
There are also no beams and no columns and the waterproof seams last a lifetime. The structure can be insulated by the K-13 spray-on system and adapts to a wide variety of designs and functions. It lends itself easily for expansion, enables precise customisation of door and window openings and can be used in tandem with conventional structures. The K-13 spray-on system is three-in-one, having acoustical, thermal and fireproof insulation. The insulation material includes cellulose fibre and the system complies with international standards. It is speedier in application compared to other systems and can be sprayed on surfaces to the thickness needed. The material can be applied to almost all surfaces be they metallic, concrete or wooden and bestows an aesthetic look.
Uskon has had much experience in tensile structures - a modern form of construction whose hallmark is economic distribution of force between tension and compression elements, making such structures ideal for covering large spans.
The curvature geometry gives the membranes superiority in transferring loads and providing optimum workspace and the least operating cost for the area covered. Following new technologies, tensile structure applications have come into architectural and structural uses thanks to their long-lasting strength and ability to assemble components within short periods and at low cost as well as being able to be put to re-use. They are also light in weight, cover large spans and offer translucency options while also allowing air and vapour transmission without allowing rainwater to pass through. The structures are also easy to operate. The Uskon space frame system is a three-dimensional structure with principal components comprising circular hollow steel sections (diagonal and chord members) and solid steel connectors (nodes). The resultant integrated system, despite being hyperstatic by nature, is then designed with the section of each member being allocated on the basis of the actual transmitted load, without the need for simplifying assumptions. This is achieved with the use of computer software developed by Uskon. Taken into consideration are dead loads, live loads, snow, wind and seismic loads and temperature variations. All the tubular chord and diagonal members of the space frame are subjected to axial forces, but not the bending force, and all loading is applied through nodes.
The tube components of the space frame system are manufactured as seamed steel sections of low carbon content structural steel and conform to Din 17100, ST 37-2 or ST 52-3.
The nodes are made of hot forged steel conforming to the Din 17200 grade C45. Bolts may have different diameters and material classifications as required by the forces that need to be accommodated by the space-frame members. They have metric dimensions with sections that are in accordance with design requirements and conform to Din 13.
Their strength and classification are 8.8 or 10.9, Din 267. Bolts are tightened to the nodes by means of sieves and a pin is inserted through a hold in the bolt.
Purlin stools that provide the slope of the roof are fabricated from tubular steel sections. They comprise a bolt and steel connection at one end for attachment to the space frame with a matching U section at the other end for connection to the purlins. The nodes, supports and bolts are zinc plated to an average thickness of 25 micron for protection against corrosion. The tubes are polyester powder-coated to a minimum thickness of 60 microns after first receiving an obligatory surface treatment preparation.
Erection commences only after the satisfactory completion of the substructure by the client and the erection work is carried out in strict accordance with the approved drawings and Uskon's instructions. After fabrication, each member is subjected to a non-destructive test (axial load) up to a magnitude of 1.25 times the allowed design loads.