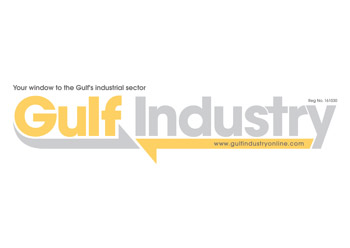
BASF, together with Faurecia, one of the world’s largest automotive suppliers, headquartered in Nanterre France, has developed a car seat back that makes use of new plastics technologies.
The third partner in the development team is Performance Materials Corporation (PMC), located in Camarillo, California, US.
BASF developed a new Ultramid (polyamide) grade specifically for this project. The new technology replaces the existing metal structure by implementing a one-piece plastic part that minimises foam and trim. The seat back weighs about 20 per cent less than conventional car seats and is approximately 30 mm thinner, making a major contribution to achieving a lightweight construction. The seat also takes advantage of the design possibilities that plastic offers, combining comfort with a modern thin-walled, high-end component affording greater design freedom and improving the feeling of space. The special features of the seat back are layers of continuous fibre-reinforced plastic which are overmoulded with Ultramid in a second step. BASF’s new polyamide grade employed here has specially selected mechanical properties, giving it tailor-made characteristics for being combined with the continuous-fibre structures.
For simulation of the crash behaviour, BASF was able to assist Faurecia by deploying Ultrasim, its simulation instrument. Specifically for this project it was expanded by the material data relating to continuous fibre-reinforced plastics and can now reliably predict the crash behaviour of components having a very high (fibre) anisotropy and fibre content.
The seat is considered a breakthrough in the construction of lightweight seats and is now ready for serial production.