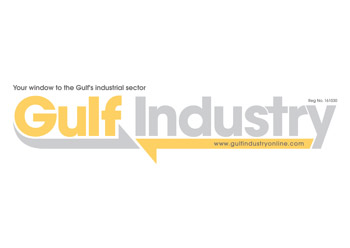

Bayer says its Makrolon polycarbonate is opening up completely new styling options in the automotive industry for the design of tailgate modules.
The company has drawn attention to its BayVision prototype concept of a complete, single-part tailgate with integrated backlite developed by Bayer MaterialScience. Unlike the conventional design involving a metal carrier and a glass window inserted in it, the part has a completely seamless outer skin consisting of coated polycarbonate. Non-transparent areas are either backprinted in a dark colour or back-injected with a black frame material using two-component injection moulding.
Volkhard Krause, head of the automotive glazing team at Bayer MaterialScience, says: “Our concept sets out to demonstrate the enormous design freedom offered by Makrolon compared with glass and metal for giving the rear of the vehicle a distinctive appearance. According to our estimates, a weight saving of around 30-40 per cent is achieved with the Makrolon part compared with the same part made of metal and glass. Apart from that, the integration of functions opens up considerable cost-cutting potential for the manufacturer,” explains Volkhard Krause, head of the automotive glazing team at Bayer MaterialScience.”
The concept, which was shown for the first time at K 2010 in Dusseldorf, aims to lead on to concrete projects with systems suppliers and OEMs.
High integration potential
The backlite is part of the polycarbonate outer skin and, as such, is directly integrated into the tailgate. Unlike conventional glazing units, it no longer has to be glued in, thus simplifying assembly and logistics. There is, for example, no need to apply adhesive or precisely adjust the glass window before bonding.
A rear spoiler and two styling lines – one of them directly in the area of the backlite – have been moulded directly on to the prototype part. “Both these features would have been impossible to produce in this way with metal and glass. The spoiler, for example, would have had to be mounted separately,” says Krause. Tail lamps, indicators, brake lights, license plate lights and the raised brake light are located behind the polycarbonate outer skin. The relevant fixings and guides can be directly integrated using the two-component back-injection method.
The basic transparency of polycarbonate would also allow the vehicle license plate to be accommodated behind the outer skin. Instead of separately mounted locks and door handles, light sensors could also be installed behind the outer polycarbonate skin for opening and closing the tailgate. “Both these features,” says Krause, “would underscore the homogeneous appearance of the part as a whole and enhance its stylish look.”
Hybrid technology
A tailgate manufactured exclusively of polycarbonate would not be stiff enough to meet all the load specifications. Bayer MaterialScience’s automotive glazing team has therefore developed a new concept based on plastic-metal composite technology (hybrid technique), which enables the typical stiffness requirements for tailgates defined by the automotive industry to be met.
The concept is based on reinforcing ribs of polycarbonate or its blends (e.g. PC+ABS), which are moulded on to the inside of the tailgate. Simple strips of sheet metal are inserted in the grooves between the ribs and bonded with an elastic adhesive. The elasticity of the adhesive evens out among other things the differences in heat expansion between the metal and the amorphous plastic.
The concept is highly flexible in terms of design because the reinforcements can be positioned exactly where they are needed. Calculations have shown that only a few metal inserts are required to achieve a high level of stiffness. In addition, simple – ie unformed or minimally formed – metal inserts can be deployed according to their optimum loading direction.
“Large steel inserts are not required in this concept, reducing weight significantly. Moreover, the tailgate can be connected via the metal inserts to load-carrying elements such as locks, hinges, or dampers on the bodywork,” explains Ulrich Grosser, project manager in applications development at Bayer MaterialScience.