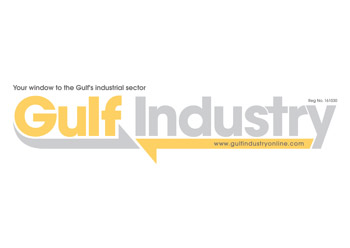

The production of precision metal components through casting and machining involves considerable skill and the use of sophisticated machinery, requirements that Metals of Bahrain (MEBA) WLL has been able to fulfil well.
So well, in fact, that its facilities have produced components for discerning Western buyers, while also fulfilling orders for prominent companies within the Gulf
MEBA commenced operations as a machining centre in 1992, but it was only in 2003 that it took upon itself the additional responsibility of foundry work. The company has the capability to produce a total of 70 tonnes per month of components manufactured from various exotic alloys, and has advanced from working at half capacity in 2003 to 60 per cent in 2004.
The product range covers pump impellers, valves, crusher parts, well service parts, heat-resistant grills, gear housing, tension-bearing items, stabilisers, bushes and flanges. The alloys cover the ferrous and non-ferrous ranges. The raw materials are sourced worldwide, phosphorous bronze coming from New Zealand, brass from Italy, bronze from Saudi Arabia and stainless steel and mild steel from the Arabian Gulf markets.
Brought in as ingots or scrap, the raw material is converted into alloys to meet the specific requirements of customers.
MEBA has installed a spectrometer built by Thermo Electron Corporation, Switzerland, for analysing the chemical composition of metals, which assures customers they will receive the very exact grades they requested for their alloys. MEBA’s spectrometer tests 16 elements in alloys of steel, stainless steel, bronze and brass. While the company has the capability of producing components from a number of alloys, it mainly works with bronze and stainless steel.
“We are an ISO 9001-certified metal centre with two main divisions, namely the foundry division where we accomplish melting and casting, and the machining division, where products already cast are fine tuned to the required finish and shape,” says marketing manager Adel Dawood.
“We have two induction furnaces that use electricity and work more efficiently than diesel and gas furnaces and are more environmentally friendly. For casting, we use chemical-bonded sand. Sometimes we supply as cast, if the customer wants it that way, at other times performing machining after the casting or just the machining if the casting has been done elsewhere.”
Integrated with the casting process is the pattern-making facility for making tools and moulds for various items. Star equipment at the facility is a pattern-making router from ShopBot, USA.
Less than 10 per cent of the company’s production is supplied to Bahrain customers and these include oilfield servicing companies as well as establishments undertaking melting of aluminium such as Garmco and Bahrain Atomisers. It has also fabricated a gear case for Aluwheel.
MEBA’s biggest market is neighbour Saudi Arabia, which accounts for 60 per cent of all its production. Saudi firms usually take pump parts, mainly impellers, and have them assembled at their pump-manufacturing plants. A major buyer is Saudi Mechanical Industries, Riyadh. Another company, Saudi Ductile Iron Pipe Factory (SADIP), Dammam, is a major importer of MEBA pipefittings. MEBA machines the fittings after it receives the casts for them from its sister company, Riyadh-based Saudi Cast.
MEBA has started making moulds and casts for earth-moving equipment for traders and end-users in Dammam and Riyadh and other Gulf markets.
As well as marketing assistance, MEBA receives technical help through its sister-company relationship with Saudi Cast, reverting to it when confronted with issues concerning casting. Saudi Cast itself is a distinguished company that has technical collaborations with two major societies - Casting Technology International, UK, and the American Foundry Society.
MEBA is proud that its products have attracted the attention of Western buyers. The company is supplying bronze rings and other valve components to the Scottish manufacturer Glenfield Valves. The entire casting and machining work is done at Meba’s facilities in Bahrain.
MEBA has also been supplying valve parts to another British company, Aqua-Gas in Corby. The parts supplied are mainly the valve body and these are first cast at Saudi Cast, and then machined at MEBA.
The company has been successful in bagging orders from US companies, two of which are Goulds and National Pumps. Both import MEBA-made pump impellers.
“We have succeeded in winning new orders and repeated orders because we select the best equipment and workforce,” says Dawood. “As everyone knows, you may have the best machines but of what use are they if your workers lack the skills to operate them?” MEBA’s workers have long experience in major establishments within the Middle East and beyond.
Among machines they handle are the Pittler CNC auto lathe with a Siemens controller; Wickman multi-spindle auto lathes up to 44 mm; SAIC single-spindle auto lathe up to 30 mm; Rossinik rotary transfer centres, both vertical and horizontal; Arcardini rotary transfer centres; 230-tonne Triulzi high-pressure die casting machine; a trimming press, bar cutter and billet heater and nickel chrome plating and galvanising equipment.
Facilities at the company include an EDM facility for tool making; gang drills and milling, surface grinding tools; component polishing vibrator; assembly units and custom-built machinery; component hydraulic pressure testing; annealing and a tool and die-making facility.
The company works with ferrous alloys including carbon steel ASTM A 216, A 532; low alloy steel ASTM A 217, A 487; stainless steel ASTM A 744; duplex stainless steel ASTM A 890 and heat-resistant steel ASTM A 297. Its non-ferrous alloys are gunmetal bronze, phosphorous bronze, aluminium bronze, nickel bronze, silicon bronze and aluminium of LM 4, LM 6 and LM 24.
The biggest item the company has cast was of size 100 kg, although MEBA can easily go up to 150 kg. Saudi Cast does casting of 500 kg on a regular basis, having a furnace of a capacity of a tonne and a half, against MEBA’s capacity of well lower than that in each of its furnaces. The furnaces that MEBA has installed are suitable for the kind of small-dimension orders it has been receiving, but it plans to acquire the capability in the near future for executing orders for larger components. Dawood says the company is assessing prospects for such orders and determining what metal grades and weight its customers would seek.
The challenge of making large tools could already be at its door. Although it does not have a single furnace to handle more than 150 kg, the company is negotiating with a prominent Bahrain company to be entrusted with the work of producing a 300-kg component. If it receives the assignment both furnaces at MEBA will be utilised for the operation, and Dawood says working on two to produce one component would be a very intricate operation.
MEBA’s management plans to build a large covered shed to accommodate future expansions. Dawood says current prices in international markets are conducive for growth as long as fuel costs in Bahrain are low. And while there are several competitors in the GCC, he does not see that by itself as an impediment to growth. “We shine on the basis of our workmanship, our facilities and our quality production,” says the official. “The problem is when competitors offer cheaper products that do not have the same quality as ours and manage to deceive customers who will eventually realise they’ve been had.”