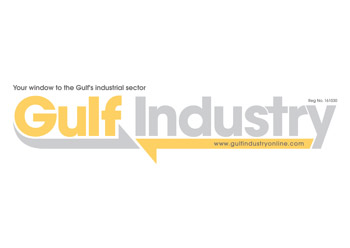

If one looks back across the nearly two decades that Gulf Aluminium Rolling Mills Company (Garmco) has been in operation, one sees two striking elements in its history.
The tremendous surge in production and a shift in export markets.
For one thing, the initial production capacity of 40,000 tonnes per year (tpy) has been stepped up to 145,000 tpy, thanks to a series of upgrades and expansions over the years.
The second striking aspect in Garmco’s spectacular progress has been the changing market scenario. For many years, the Far East was its biggest importer, but, for the first time, the Middle East replaced it in 2003, accounting for around 42 per cent of total sales. That is a sizable figure, considering the company’s worldwide sales that year were 123,628 tonnes. The radical development was not unexpected in view of the fact that the Middle East is now home to a growing number of industrial establishments, including some of the world’s largest. Saudi Basic Industries Corporation (Sabic), for example, has been propelled into the very top echelons of petrochemical companies and boasts a 2003 sales turnover of $12.5 billion. Sabic is also one of the shareholders of Garmco, holding a significant stake of 30 per cent. The main shareholder is Bahrain at 38 per cent with Industrial Bank of Kuwait 17 per cent, Gulf Investment Corporation six per cent, Iraq five per cent, and Oman and Qatar, two per cent each, holding the remaining stock.
“Sales to the Middle East constitute a competitive advantage because proximity leads to lower transportation costs. So we prefer to sell there,” says Garmco administration manager Adel Hamad. The company spends around $5 million for shipping its products to all regions. The Middle East market stretches from Morocco to the Indian subcontinent and imports quality flat-rolled aluminium from Garmco facilities. Other company products going there are coil for paint lines, automotive applications, lithographic plate manufacture, electronic industries; foil reroll; sheet for major engineering and construction projects and circles for both small and large producers of hollowware.
In the wake of advancing Middle East sales, the Far East now accounts for 40 per cent of the turnover with Europe contributing 15 per cent.
Between 1986, when Garmco produced its first 20,000 tonnes, and 2004 (expected output: 138,000 tpy), much happened along the way. The very first equipment enhancement raised capacity from 40,000 tpy to 70,000 tpy by 1990. Subsequently the company bought a complete aluminium factory from Alumax, in Hawesville, Kentucky, USA, and after some modernisation and improvements had it installed in 1993 for the production of cold rolled products. Total capacity shot up to 125,000 tonnes.
In another development, the company set up a foil mill of 6,000 tpy just south of the main mill in 1999 to produce household foil, semi-rigid container stock and fin stock to meet a growing demand from converters in the Middle East. Its capacity was subsequently raised to 12,000 tpy. Another expansion is in the process to raise the level to 20,000 tpy.
Today, with all the updates and expansions it has undertaken, Garmco boasts a capacity of 145,000 tonnes of coils, sheets, circles and foils. Even that high level could be overtaken before long in the face of rocketing international demand. The company has indicated it is planning its next major expansion, which it proposes to carry out in three stages, the first one involving an increase to 160,000 tpy, the second one taking capacity to more than 200,000 tpy, and the third taking capacity all the way to more than 240,000 tpy. To achieve those levels, the company has said it will use the Continuous Casting technology and increase its cold rolling capacity.
Continuous Casting will be the new technology that Garmco will introduce. “The company is working with industry majors such as Ferrostaal of Germany, VAI of Austria and Fata Hunter in Italy to put together a project which would increase capacity by 95,000 tonnes to a total of 240,000 tonnes,” said Patrick RA Beckett, commercial manager and chief financial officer, at Arabal 2004. “Bringing in this new technology will strengthen Bahrain’s position in the global aluminium industry.
“As the final product of this expansion will be manufactured through a different process, the output will have different metallurgical properties, and therefore the product range to be sold by Garmco will expand. The raw material for this expansion will be molten metal from Alba, and therefore they will not have to invest in further casting facilities.”
A significant feature of Garmco’s history was the development of a process for the hot mill that enabled it to produce high-quality, internationally acceptable canbody stock. But, because the production of canbody would reduce the overall plant capacity, the company elected not to produce can stock under present circumstances.
Among new equipment introduced recently was the direct gas-fired reverberatory furnace to melt “light” aluminium scrap having a high surface area to weight ratio such as scalper chippings.
The 12-tonne-capacity furnace features an electro-magnetic pump that circulates the molten aluminium from the main furnace chamber into a circular charge well where a molten metal vortex or swirl is formed. Light scrap is then continuously fed into the well by means of a simple vibratory conveyor and is immediately pulled subsurface by the action of the high-velocity vortex. By submersing scrap rapidly into the molten aluminium there is significant reduction of oxidation leading to improved yields.
The company also installed a third slab heating furnace linked directly to the existing hot rolling process and this addition is helping maximise hot mill output.
The pusher-type furnace, designed, manufactured, installed and commissioned by SAS, has three zones, each holding six slabs giving a capacity of 180 tonnes. The company had to make ample preparations ahead of the installation of the furnace. Extensive structural modifications were carried out to provide increased headroom in the scrap bay together with new high bay lighting and the provision of a 10-tonne EOT crane and gantry system. As space was tight, some existing equipment including the scalper system chip crusher, fane and hoppers was relocated.
Another major undertaking was the upgrade to Cold Mill No 1, which involved upgrading the PLC and replacing the mill process control computer systems. The original equipment had become obsolete, putting at risk cold rolling operations.
Cold Mill 2’s capacity was enhanced, enabling the increased tonnage produced at the Hot Mill to be processed. The enhancement came about through a combination of improved plant availability, consistency of product quality and increased mill speed.
The company’s sixth Annealing Furnace was installed in 2004 to meet the requirements of the increased cold rolling capacity. Solios Thermal-UK designed, manufactured and installed the furnace.
Garmco was given a sound foundation at the very start with Kaiser Engineering, USA, as constructor of the plant. Machinery was installed by Kobe Steel of Japan, which also undertook the start-up operation and the training of local staff at one of their aluminium plants in Japan. Garmco’s links to its neighbour Aluminium Bahrain, one of the world’s top-producing smelters, was also a great advantage. Alba supplies all of Garmco’s metal requirements, making it the largest captive customer for the smelter. Garmco officials are quick to point out it gets no special treatment in prices. “We have to negotiate hard for our quota,” said general manager Antony Lewis.
Interestingly, the 2003 sales of 123,628 tonnes fell below the 2002 figure of 125,091 tonnes, but Hamad hastened to explain that the shortfall was not a bad thing for the company. “Notwithstanding the lower sales, our earnings were higher because we were selective in accepting orders. We went in for higher-value products,” he said.
Garmco products can be categorised in terms of applications such as fin stock, re-roll, household items, paint stock, hardware for computers and appliances and hollowware. Which applications the products fit in depends on the alloys used and Garmco makes its products from a wide range of alloys.
“Sheets bring us the most income, followed by coils for the electronic industry and paint stock,” says Hamad.
Increased industrialisation in the Middle East and elsewhere means Garmco will continue to be a sought-after producer. “We are production limited rather than sales limited,” says Hamad. Now that Alba is about to complete its Potline 5 expansion, which will boost capacity to more than 800,000 tonnes, Garmco expects to receive a higher quota. Another Alba expansion is in the consideration stage, ensuring that Garmco will continue to be a powerful world player downstream.
As production levels rose, Garmco concentrated on optimising costs in its various operations to maximise income. It also recycles 25 per cent of the primary metal it uses. Those efforts have assisted in a cost decline of $178 per tonne in the last seven years.
The company’s international supplies have greatly been assisted by the presence of its subsidiaries. In effect, subsidiaries account for 60 percent of its sales in various markets. In the US, it owns two manufacturing facilities and a distributing facility, namely Midamerica Extrusions, Republic Foil, and Garmco USA. Midamerica, in Indianapolis, Indiana, operates a 3,500-tonne press with an annual output exceeding 10,000 tonnes of finished product. It has capabilities to produce complex custom designs. Republic Foil, in Danbury, Connecticut, supplies electrolytic capacitor foils worldwide. The foils roll down to 4.5 microns, the thinnest commercially produced aluminium foil in the world. Additionally, Republic Foil supplies a range of items to the packaging industry including eyelet stock, fin stock, cable wrap, specialty bright sheet and foil as well as stock for lithographic applications.
In the Far East, Garmco has a subsidiary based in Hong Kong, which since 1991, has contributed much to serving the markets of the region. The Hong Kong office was the first step in the company’s drive to penetrate key markets in the region. The second step was the establishment of two service centres in Singapore and Melbourne, which were provided with fabrication equipment, enabling them to supply both the local and Far East markets with fabricated sheet products. These two subsidiaries constitute 15 per cent of the Bahrain company’s total sales. And recently a sales office was opened in Shanghai.