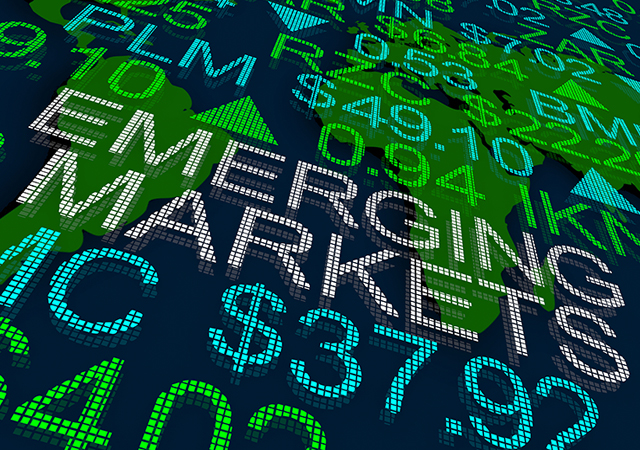
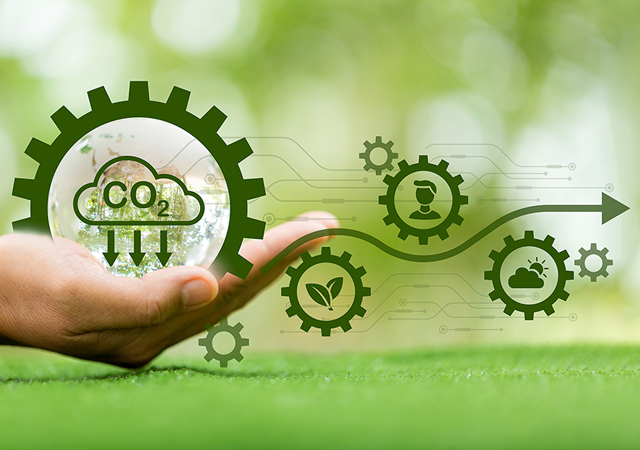
US manufacturing is undergoing significant transformation as companies recover from the pandemic. Challenges include reducing greenhouse gas emissions, retaining talent, managing supply chain disruptions, reinventing business models, and protecting operations from cybersecurity attacks, according to a report by PwC.
However, the nation is also emerging as a viable location for onshoring and nearshoring, rethinking global supply chain footprints, and recalibrating business models through digital technologies. These trends are expected to intensify in 2024, requiring manufacturers to adapt to compete.
Here are six increasingly important trends that can impact industrial products sectors through 2024 and beyond — and what manufacturers should do to stay ahead of them, according to PwC.
THE NEW MANUFACTURING EMPLOYEE EXPERIENCE: WHY CREATING ONE NOW IS SO IMPORTANT
Manufacturers are rethinking their strategies to attract and retain talent in the industrial labor force, as the need to fill jobs increases. A PwC Pulse survey revealed that seven in ten industrial products companies believe talent acquisition and retention pose a risk to their organisations. With about half a million manufacturing jobs unfilled, it is crucial to improve retention rates and attract more talent.
The US is experiencing a historic wave of investment in new factory construction, making it essential to change the industry's workplace image from repetitive and physically taxing to one that offers technology adoption and career growth.
To improve the employee experience, manufacturers should expand total rewards, support well-being and purpose in the workplace, and provide upskilling and training for upward career mobility. If internal use software is developed and meets certain IRS tests, the cost may be offset by research and experimentation credit.
Where should executives look to build a stronger, more sustainable workforce?
Chief Human Resources Officer (CHRO): In order to attract a new generation of talent — and to retain valuable existing employees — human resource leaders should take stock of what their workers want, especially frontline employees. Regular surveying of workers is critical to knowing what to offer both existing workers and to lure new employees, especially those with the technology skills that are increasingly needed by most manufacturers.
Chief Executive Officer (CEO): Promoting a culture of meaningful and satisfying work throughout the organisation is both a bottom-up and top-down process. It’s important for the CEO to advocate attractive working conditions and nonfinancial benefits to address needs and raise morale for employees.
STRENGTHEN CYBERSECURITY AS ATTACK SURFACE GROWS?
Cyber threat actors are targeting manufacturers, with over 600 ransomware attacks in 2022, nearly double those in 2021. The trend is not slowing down, as attackers are expanding their attack surface, particularly across operational technology networks, stated the report.
The adoption of new connected technologies, such as AI, machine learning, 5G, IIoT, and quantum, and the mainstreaming of internet-connected products and services can expose vulnerabilities.
As a result, manufacturers are urged to close the gap between OT and IT teams, extend OT cyber protection initiatives, invest in cybersecurity technologies, and ensure connected products are certified with industry standards. This investment may qualify for research and experimentation credit, potentially covering increased internal development costs.
Where should executives look to bolster cybersecurity?
Chief Information Security Officer (CISO): As manufacturer attack surfaces widen, CISOs should confirm that employees are apprised of — and trained to limit — cyber risks. In particular, they should take special efforts in closing the collaboration gap between IT and operational technology teams that often exists at many plants.
Chief Operating Officer (COO): Making sure that internet-connected assets are tracked and cyber-proofed is increasingly becoming the COO’s responsibility. COOs also should see that factory floor workers receive continual cybersecurity training, and work closely with IT teams to collaborate on cybersecurity initiatives and protocols.
BACK IN THE USA: A NEW GOLDEN ERA FOR US MANUFACTURING?
The US is experiencing a factory build-out boom, with annualised investment in factory construction reaching $195 billion as of June 2023, more than double the $78 billion invested in June 2021. This trend is fueled by federal and state policies and incentives, such as the Infrastructure Investment and Jobs Act, the Inflation Reduction Act, and the CHIPS Act, which make domestic production more attractive and secure, claimed PwC.
This investment coincides with a reassessment of global footprints, particularly in China, and a shift towards reshoring and nearshoring production by US manufacturers and inbounding by foreign companies.
Geopolitical risks and rising labor and shipping costs have also impacted far-flung sourcing. Manufacturers are exploring digital supply chains to create a more agile and resilient supply chain. However, the global shortage of powerful microprocessors, particularly due to generative artificial intelligence, will likely persist as a persistent supply-chain challenge.
THE NEW AI WAVE: ARE MANUFACTURERS READY TO DIVE INTO GENAI?
Manufacturers are increasingly investing in digital solutions like data analytics, AI, and machine learning to improve operations, supply chain, and customer experience. PwC's Pulse survey shows that over two-thirds of industrials plan to invest in new technologies over the next 18 months, with 40 per cent planning to invest in GenAI, according to the report.
GenAI can accelerate digital transformation by securely accessing and leveraging a company's unique data and intellectual property. It can lead to cost-savings, improved product quality, and competitive strength.
However, GenAI also carries risks and should be applied responsibly. To identify the most effective use cases, manufacturers should conduct a thorough vetting process, improve data collection processes, acquire talent, and ensure cybersecurity protections are in place.
ELECTRIFICATION OF TRANSPORTATION: A LONG AND BUMPY ROAD
The shift towards electrification of transportation is transforming automakers, who are rapidly developing new business models to support connected, autonomous, and electric vehicles while maintaining their traditional internal combustion engine businesses. EV penetration is expected to rise from 2 per cent to 30 per cent by 2030, with commercial EV fleets being adopted by many companies and governmental entities.
However, the transition has been challenging due to delays and competition from EV-only companies. The success of EV mainstreaming is closely tied to the development of a coast-to-coast charging network.
Federal and state policies, such as the Infrastructure Investment and Jobs Act, Inflation Reduction Act, and CHIPS Act, are subsidising increased electric vehicle purchase costs and production plant investments.
MEASURING AND REDUCING MANUFACTURING GHG FOOTPRINT
US manufacturers are preparing for a net-zero future, with many setting greenhouse gas reduction targets and creating green operating models. However, 52 per cent of industrial products companies believe not meeting sustainability requirements poses a risk to their businesses, revealed the report.
Manufacturers can lead by demonstrating how other industries can measure and report emissions, with the engineering and construction industry demonstrating how asset owners can track, cut, and report emissions by providing net zero services and building sustainable operating models. Many countries are adjusting their tax systems to influence climate-impacting business decisions.
Where should executives look to ramp up efforts to monitor — and reduce — GHG emissions?
Chief Security Officer (CSO): Most chief sustainability officers should focus squarely on getting Scope 3 emissions monitoring and reduction right. The ability to do so well will likely become an increasingly important differentiator among many business stakeholders.
COO: Companies should intensify efforts to scrutinise emissions footprints of many supplier tiers in order to consistently track and reduce Scope 3 emissions. Likewise, they should account for emissions produced upstream in the value chain. For many manufacturers this can add a new layer of complexity to supply chain due diligence.