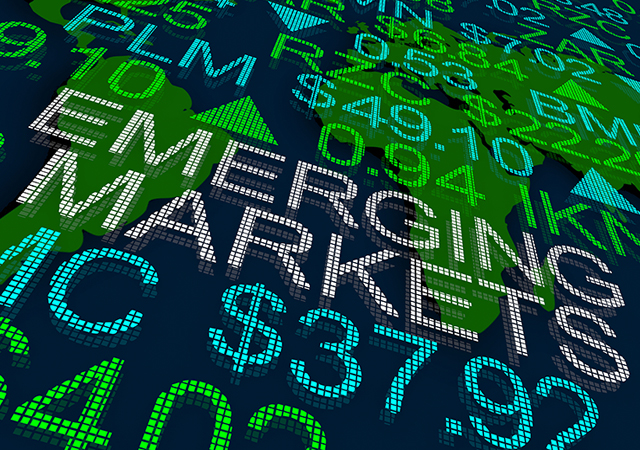
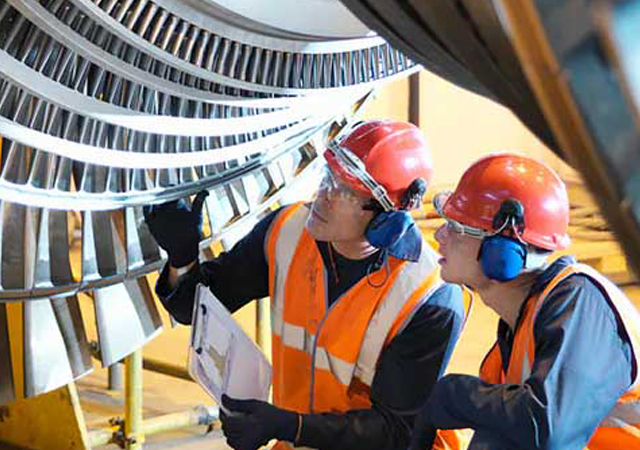
Industrial manufacturing trends in 2024 and beyond will be influenced by technological advancements and government initiatives like the US Chips and Science Act, Infrastructure Investment and Jobs Act, writes Margaret Lindquist, Content Strategist at Oracle.
The industry will respond to skilled labour shortages, supply chain disruptions, and sustainability commitments by investing in "smart factory" initiatives for better planning, design cycles, and supply chain visibility.
The manufacturing industry is transitioning from machine-based assembly lines to "smart factories" using robotics, IoT, data analytics, and AR technologies, known as Industry 4.0, driven by automation and connectivity.
Key industrial manufacturing trends:
1. INVESTING IN TECHNOLOGY
Industrial manufacturers that increased their technology investments during the pandemic were better able to weather the downturn. Deloitte's 2023 outlook survey revealed that leading manufacturers are investing in robotics and automation to speed up manufacturing, reduce costs, and alleviate labor shortages. Data analytics is being used to improve forecasting and spot supply shortages before they affect the manufacturing line. IoT is being used for improved manufacturing, supply chain tracking, and product maintenance, stated Lindquist.
Implementing Industrial IoT
The Industrial Internet of Things (IIoT) involves networks of physical objects embedded with sensors and software that collect and exchange data over the internet. It helps manufacturers monitor factory floor robots, track assets in supply chains, and monitor machine temperature, humidity, and vibration frequencies. With 5G technology, the percentage of IIoT implementation is expected to reach 50 per cent by 2025.
Accelerating Digital Transformation
A survey by IndustryWeek and Oracle shows a growing competitive gap between manufacturers investing in digital capabilities and data-driven processes. The top priorities for respondents include improving efficiency, production development, responsiveness to market demands, and deepening customer relationships. Half of the respondents believe working in a more virtual environment will be a future requirement. The industry is also focusing on digital transformation initiatives like microfactories, automation, and early visibility of potential disruptions.
2. ATTRACTING AND NURTURING TALENT
US industrial manufacturers face labor shortages due to faster retirements, higher pay, and difficulty in attracting specialists for Industry 4.0 technology. McKinsey predicts a 30 per cent decline in traditional labor demand over the next decade, while technical skills demand will increase by 50 per cent. However, manufacturers struggle to find essential workers like machinists, welders, metalworkers, and production supervisors.
Implementing Employee Retention Strategies
According to the report, the US manufacturing skills shortage could lead to 2.1 million unfilled jobs by 2030 and cost the industry $1 trillion in 2030. To address this, manufacturers are planning to raise wages, reskill employees, and develop recognition programs. A 2020 survey found that employees who feel valued at work are highly motivated, satisfied, and would recommend their company to others. Modernising facilities, introducing robots and drones, and promoting hybrid and remote work are also being implemented. To retain their next-generation workforce, manufacturers must create an environment of continuous learning and nurture careers, despite the negative perception of the industry.
Overcoming Workforce Shortages through Reskilling
A 2020 study by The Manufacturing Institute and the American Psychological Association revealed that young employees are attracted to employers who invest in their skills and career advancement. Employers should consider reskilling programs like live courses, recorded videos, and augmented/virtual reality. Programs like America's Cutting Edge and Creators Wanted help connect people with training, job openings, and new career pathways.
Diversifying the Workforce
Manufacturers face challenges in finding entry-level and technically trained workers for production positions. To address this, they must attract more women and underrepresented ethnic groups. Women currently make up less than one-third of the manufacturing workforce, while Black, Asian, and Latinx employees make up 36 per cent. The Department of Defense is funding a $6.2 billion initiative to train and reskill the future workforce, while a National Association of Manufacturers campaign provides mentorship to women, reported Lindquist.
3. INVESTING IN SUSTAINABILITY
According to a 2023 US Environmental Protection Agency report, the manufacturing and raw materials industries were responsible for 23 per cent of greenhouse gas emissions in the US. Although the industry has made progress in recent years to reduce those emissions, it still has a long way to go. Manufacturers need to evaluate their entire supply chain and seek opportunities to reduce waste, increase supplier diversity, and prioritise the use of fuel-efficient and electric vehicles on the factory floor and for product delivery.
Prioritising Sustainability and Carbon Neutrality
A 2022 study by Climate Impact Partners shows that 42 per cent of Fortune Global 500 companies have achieved a significant climate milestone or committed to do so by 2030. While carbon neutrality is a good first step, setting emissions goals throughout the supply chain is crucial for achieving zero carbon goals. Some manufacturers are investing in smart building technologies, renewable energy sources, and electric vehicles. A 2021 McKinsey survey found that 22 per cent of manufacturers generated value from sustainability initiatives over the past five years, with 40 per cent expecting to generate value in the next five years.
Prioritising Corporate Social Responsibility
Corporate social responsibility (CSR) is a self-regulation approach by companies to ensure positive environmental, consumer, employee, and community impacts. It involves environmental sustainability and social progress, such as recycling and reducing waste. Manufacturers' actions benefit not only the planet and its inhabitants but also the bottom line. A 2022 survey by Lab42 found that 84 per cent of respondents are willing to pay more for products from companies they perceive as socially responsible.
4. REEVALUATING THE SUPPLY CHAIN
In 2023, it’s no longer enough for manufacturers to have visibility into the actions of their suppliers and customers. That visibility needs to extend to their suppliers’ suppliers and their customers’ customers. Successful manufacturers will invest in digital supply chain capabilities that can provide better insights into the functions of each stakeholder along the chain and enable each participant to make better decisions about material sourcing and customer demand, revealed Lindquist.
Solving Supply Chain Disruptions
Industrial manufacturers are shifting their raw material and product production locations due to supply chain disruptions. Since the 1960s, manufacturers have sourced materials from lower-cost countries, but are now shifting back due to rising labor costs, shipping costs, and exchange rates. A 2021 survey by Thomas revealed that 83 per cent of North American-based manufacturers are likely to reshore at least part of their operations. This is part of a larger trend to diversify their supplier base, with over half of manufacturers seeking alternative suppliers in 2021.
Shifting to Product as a Service
Manufacturers can capitalise on market opportunities by offering products as a service, charging fixed or usage-based prices. For instance, car manufacturers offer vehicle usage for an enrollment fee and monthly subscription fee. Cloud computing is a product as a service, with software developers delivering applications and infrastructure over the internet as a subscription. Other manufacturers offer product installation, monitoring, and maintenance services. Advantages include regular revenue streams, cross-selling opportunities, and valuable customer data for product development, said Lindquist.
5. BUILDING THE FACTORY OF THE FUTURE
The future factory will be highly automated and efficient, with drones providing workers with inventory and machine health data. Inaccuracies and human error will decrease, and AI, machine learning, IoT, and robotics will play a larger role in warehouses and factories. The smart factory will have a solid back-office base with financial, production, and planning software capable of handling vast amounts of data.
Modernising Through ERP
Industry 4.0's potential lies in manufacturers understanding technologies that simplify processes, collect accurate information in real time, and reduce costs. Many legacy ERP, SCM, and PLM systems are outdated and disconnected. Modernising ERP systems to cloud services is crucial for access to updates, security controls, and on-demand application scaling. Integrated cloud applications provide visibility across functions, enabling manufacturers to adapt to Industry 4.0.
Using Data-Driven Decision-Making
Manufacturing systems generate vast amounts of data, such as offshore oil platforms, which are used to prevent spills and equipment failures. As data flow increases, manufacturers require sophisticated software to analyze and extract insights. Analytics software is a top focus for 60 per cent of companies, while 37 per cent prioritise data quality issues. Digital twins, digital representations of manufacturing facilities, processes, and products, help business leaders make informed production decisions and assess product quality before investing in physical assets, claimed Lindquist.
Adopting Automation and Robotics
Automation in manufacturing is increasing, with adoption rates for robots, cobots, drones, and autonomous vehicles rising. North American orders for workplace robots increased by 25 per cent in Q2 2022. The global market for industrial robots is expected to grow at a 10.5 per cent CAGR between 2023 and 2030. The global cobot market is expected to reach $8 billion by 2030. The agricultural robotics market is predicted to grow from $7.6 billion in 2022 to $21.1 billion by 2028.