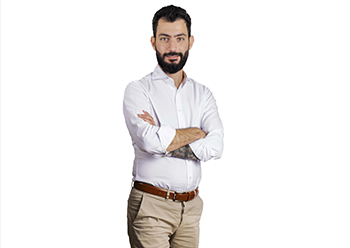
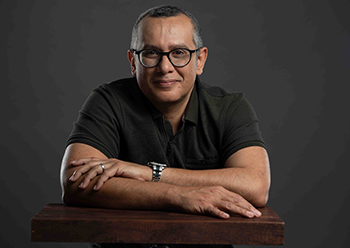
As we’ve all learned by now, there’s no single technology that will provide a silver-bullet solution to the challenges of sustainability. However, there are technologies that can make a lot of important contributions, in different ways and in different places, to get us to where we need to go.
One such technology or group of technologies, is the concept that’s traditionally referred to as the Internet of Things (IoT). In truth, it’s a term that struggles to capture the full range of what these types of systems can now do. We’re rapidly evolving towards a new paradigm of hybrid-edge, cloud-connected architectures that achieve much more than just collecting and sharing data. The future of IoT involves digital models for every element of manufacturing, which provide new levels of monitoring, analysis, and real-time control. It also involves embedding machine learning capabilities within hardware that are capable of complex image analysis, and responding to changes rather than simply recording them.
Everywhere you look along the lifecycle of products, from supply chains to manufacturing, to what happens when something leaves the production line, you’ll find these technologies enabling a different way of working. In the process, they are turning one of the most important concepts in sustainability from futuristic vision to practical reality. Our new IoT technologies are enabling the circular economy to finally take shape.
Customers don’t ask us for IoT in the same way that Chief Technology Officers don’t ask for, ‘some IT’. They think in terms of specific business outcomes and how they can monitor, control, and optimize their business processes to get those outcomes. If we’re serious about making a circular economy happen, then there are a lot of relevant outcomes that modern, cloud-based architectures can contribute towards. They include extending the lifecycle of products and their components, keeping them in use through recycling and refurbishing, and increasing energy efficiency to the point where circular manufacturing can run entirely on renewable energy. Here are five of the most significant ways in which the new paradigm in cloud connectivity is already driving the circular economy forward.
Questioning manufacturing’s sacred cows
There’s a lot of dogma in manufacturing; a lot of principles that are set in stone and rarely questioned, because they’re a safety net for protecting things that are important to a manufacturer’s bottom line. Traditional manufacturing lore has it that it’s rarely worth the risk of shutting equipment down. Things are more robust and more efficient when you keep them running – and running at full speed. Concern about reliability issues constrains the way manufacturing operates because everything has to be optimized around keeping processes going. This doesn’t just use a lot of energy – it also shuts down a lot of the potential for innovation.
Cloud-connected manufacturing changes the game in two important ways. First, by digitally enabling manufacturing, capturing, and analysing valuable data, it removes the mystery around reliability issues. Cloud connectivity shows what fails and why – delivering insights that enable predictive maintenance to solve the issue rather than running the entire operation in a certain way to prevent it. This responsiveness has greatly increased in recent years thanks to the Hybrid Edge, which puts decision-making technology within a factory itself, so that it’s able to respond to data immediately rather than just uploading it to the cloud. Second, cloud-connected manufacturing provides a new level of data granularity that you can feed into machine learning models to identify exactly what the optimum speed and the optimum runtime for a piece of equipment are. AWS IoT SiteWise and AWS IoT SiteWise Edge work with a broad and deep set of partners to create data-driven insights, and deliver them via drag-and-drop, no-code dashboards and intelligent applications. These make insights more accessible and more actionable to manufacturers.
The data collected through these types of applications enables manufacturers to build detailed digital representations of factories, known as digital twins. Created through tools like AWS IoT TwinMaker, these enable manufacturers to monitor, control and optimize every aspect of production in real-time. They also enable them to experiment with different processes and analyze the outcomes, while avoiding any real-world impact on production, profit or quality. They act as a key enabler of innovation.
When manufacturers start applying smart manufacturing technology in this way, they get immediate cost optimization benefits in terms of energy efficiency and reduced maintenance due to fewer running hours. There are big advantages in terms of compliance, hitting sustainability targets and reducing an operation’s energy use. And with costly barriers to innovation removed, the way is clear to test and scale more circular manufacturing processes that make greater use of reclaimed and recycled components.
Taking a closer look at the chemistry
Manufacturing works to a lot of fixed formulas that have been proven to deliver the quality and durability of product that’s required. These formulas are often built around using virgin materials, with a high level of purity, and applying a lot of heat to removing moisture from those materials. The formulas exist because they work – but they clearly restrict the scope for using recycled materials, and for improving energy efficiency. And just because they’re one way of getting to an outcome doesn’t mean they’re the only way.
Using sensors and cloud connectivity, we’re able to get under the surface of the chemistry that takes place in manufacturing, understand what’s really happening – and what’s really required at each stage. When we applied smart manufacturing to the cement industry, we were able to help manufacturers identify the optimal amount of time for heating, to avoid under or over-cooking clinker (a key ingredient of cement). Using digital twins, we could assess what level of moisture content they actually needed to remove, to enable the downstream processes to work properly. As a result, we were able to significantly reduce energy use and the environmental footprint associated with cement production.
As we move onwards into the circular economy, taking a closer look at the chemistry of materials used by cloud-connected enterprises can do a lot more. We can analyse the impact of using slightly different materials, from different sources, to those we’ve used in the past. We can use sensors to monitor how these different materials behave from the start of the process onwards, using Edge technology to adjust things as required. A lot of our work in manufacturing involves helping organizations experiment with a higher proportion of recycled materials. Our goals are to maintain yield, quality and operational efficiency while pushing this transition as far as we can. We need to know about the durability and product grade that’s coming out – and ensuring that what we’re producing through a more circular economy will have the extended lifecycle that we require.
Monitoring increasingly varied supply chains
Constructing digital twins from cloud data has a huge role in optimizing processes within factories – and experimenting with the use of new materials. It’s also got a big role to play in evolving supply chains. The automotive industry is leading the way here, as it takes a circular approach to recycling Electronic Vehicle (EV) batteries through gigafactories such as Northvolt Ett in Sweden. Companies are using real-time digital twins of their entire supply chains so that they can understand where materials are coming in, what the ship times are at each stage, where they incur risks of shortages and what backup plans they can put in place. This gets very granular, down to the levels of sensors in trucks and tanks to monitor levels. Digital twins help to visualize alternative sources of supply, test different scenarios, and give organizations the forward visibility and confidence they need to move towards a circular approach with more varied supply chains than in the past.
Tracking the ongoing lifecycle of products
Tracking the ongoing performance of products, and being able to connect this back to precise manufacturing conditions, is another area in which the auto industry is leading the way. Because there’s so much value contained in an EV battery, it’s important for auto manufacturers to monitor how they perform. If they detect patterns of deteriorating performance over time, they can trace that back to the conditions in which a batch of batteries were produced – and determine if they need to recall or update those batteries. This matters in terms of customer satisfaction and loyalty – but it also matters a great deal in the context of the circular economy.
The lifecycle of a battery doesn’t end when it’s recalled. That’s the moment when it becomes a resource to be recycled back into the supply chain – and at that point, understanding what’s happening within the battery becomes crucial. Thanks to sensor data and traceability, we know the reason for a recall – and that provides a rapid shortcut to recycling that battery as part of the circular economy.
Of course, circularity doesn’t have to involve materials being re-used by the same organization that used them the first time around. In the consumer electronics industry, cloud insights enable manufacturers to construct business models around how long chips and other elements last – and how you can realize value from them after that. Even when an organization isn’t re-using the components itself, cloud data still prepares the ground for others to do so.
It's also true that circularity doesn’t have to involve recalls, in order to extend the lifecycle of a product. Elevators are a great example. You don’t want to have to recall elevator cars too often. Instead, you want to keep them in service in a way that doesn’t compromise their performance and safety. Kone is a great example of an elevator company that’s doing precisely this, using sensors and modelling to predict and prevent failures like door jams and send service teams out proactively.
Ensuring significant change through scalability
If we’re to build a circular economy, it’s not ultimately enough to innovate in a few outlier areas of manufacturing or the supply chain. If we want to change the way that businesses use resources to drive growth, we need scalability. Enabling that scalability may well be the most significant IoT-related contribution of all.
Dashboards and digital twins enable organizations to optimize performance based on learnings from different environments – and to do this in real-time, remotely. You can benchmark one process against another, troubleshoot problems and then feed solutions into multiple factories automatically. Hybrid Edge technologies are able to respond to alarms and changes of status immediately, by connecting these to factory automation and robotics, with big gains in terms of efficiency and optimization. It all means that, once steps towards a circular economy are validated in one location, they can be rolled out quickly across others. Modern, cloud-based architectures enhance the economies of scale that ensure one productive gigafactory designed around circular economy principles becomes a chain of productive gigafactories designed around circular economy principles.
IoT is quickly changing our view of what’s possible when it comes to turning resources into growth. It’s also ensuring that change of mindset quickly turns into a change in reality.