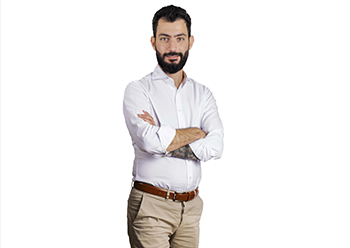
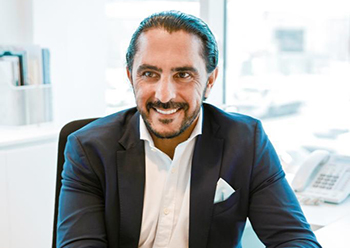
The first industrial revolution was powered by mechanisation; the second by the assembly line and mass production techniques; and the third by computerisation, automation, and lean management. Now, the convergence of connectivity, low-cost sensors, big data and advanced robotics is creating the cyber-physical production systems that will be the hallmark of Industry 4.0.
The use of robotics in manufacturing, warehousing and other sectors is increasing, playing a critical role in modern-day living. According to estimates, the Middle East warehouse automation market is expected to reach $1.6 billion by 2025 owing to strong macroeconomic and industry growth drivers e-commerce fulfilment and rising labour costs. 77% of companies are seriously looking at automated warehousing systems and are creating a plan to maximise data-driven performance to better predict demand. These insights are what will enable an organisation to configure and adapt its equipment, cobots and labour to fulfil ever-changing and complex orders, especially now that e-retail has boomed unprecedentedly.
Demographic change, spike in product demand, the accompanying high demand for logistics solutions and labour shortages are some of the other challenges that the manufacturing sector faces today.
The Middle East market has unique characteristics and challenges that can impact the effectiveness of current warehousing automation solutions. Some of the critical limitations include a lack of skilled workforce, varying storage requirements that differ from industry to industry, limited infrastructure, the hot and dusty environment etc.
To address these challenges, robotics and automation come to the rescue. Particularly within the realm of manufacturing, enterprises are progressively employing these technologies to streamline processes, enhance efficiency, and address evolving market demands. In fact, as per a Deloitte report, 62% of manufacturers intend to integrate robotics and automation in 2023, aiming to enhance operational efficiency.
Some trends for the use of automation & robotics in the manufacturing sector include:
Robotics for everyone: A drive to make robots more user-friendly is gaining momentum, targeting individuals without coding or software engineering backgrounds. This endeavour emphasises user-intuitive experiences, simplified setup procedures, and collaborations with low-code or no-code technology, all aimed at facilitating robot operation and control. This democratisation of robotics grants organisations of diverse sizes the ability to leverage automation without necessitating extensive technical proficiency. This trend also benefits manufacturers, who, as end-users of these robots, can more easily program and operate them, consequently lowering implementation costs.
AI & ML in Robotics: A notable trend in the automation and robotics sphere involves the incorporation of artificial intelligence (AI) and machine learning (ML) into robotic systems with the global AI market expected to grow twentyfold by 2030, up to nearly $2 trillion. This integration empowers robots to recognise patterns, regularities, and interdependencies from unstructured data and adapt, dynamically and independently, to new situations within the entire logistics system. Machine Learning aids in Robotics in gathering experience, anticipating situations, and expanding existing know-how without outside help – it’s how machines can make the right decision for every situation within the supply chain in just seconds. For instance, when confronted with manufacturing variations, AI-enabled robots can promptly identify these changes and provide solutions, resulting in an optimised production process and heightened efficiency.
Competitive Advantage driving automation: The prevailing global economic uncertainty and the enduring impacts of the global pandemic have significantly spurred the drive toward optimisation and efficiency. Organisations are under mounting pressure to curtail expenses, maximise productivity, and enhance the efficiency of product and service delivery. Automation emerges as a solution by automating repetitive and mundane tasks, enabling human employees to focus on intricate and value-added undertakings.
Fully automated robotic item-picking solutions, such as ItemPiQ, can help companies to reduce operational costs, retain flexibility and increase efficiency in their picking operation. The robot cell is designed to handle repeated piece picking, error-free, allowing companies to better cover seasonal peaks such as Black Friday and the Holiday season. Thanks to robot-based order picking, operating costs can be reduced in the long term and staff shortages overcome. Modern robotics is also dedicated to being more resource-efficient in terms of energy and time, thereby boosting production rates while simultaneously reducing operational expenditures. By harnessing automation, businesses can adeptly navigate through uncertain economic conditions and sustain their competitiveness within the market.
Bridging labour gaps: The labour shortage, especially amid the increasing demand for warehouse workers has also made companies turn to automation with robots to reduce the impact of worker shortages on their operations and to meet the consumer’s expectations. Nevertheless, the necessity for skilled human labour remains, as only certain tasks are suitable for automation or can be executed more efficiently by automated systems. Instead of completely supplanting human labour, a prevailing perspective considers automation and robots as tools that complement and amplify human skill sets. Automation is apt for repetitive and analytical tasks, diminishing the likelihood of human errors and enhancing consistency. For instance, with the help of Swisslog’s warehouse automation products, Rohlik, an e-grocery platform, was able to achieve a 2x increase in overall productivity, 3x growth in picking productivity, deliver 10% of orders in 60 minutes or less and bring its average order picking time to 1 minute. Additionally, robots can undertake hazardous or physically demanding tasks on behalf of humans, thereby ensuring workplace safety and reducing the risk of accidents.
Recent reports suggest that by 2025, autonomous robots will process up to 50% of all e-commerce orders, indicating that forward-thinking companies are increasingly turning to automation technologies to optimise. Robotics and automation clearly offer more opportunities than risks, but only if we embrace them as drivers of future growth, rather than sci-fi supervillains.