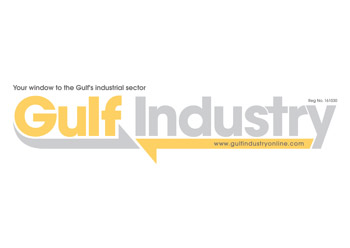

The Middle East's largest ship-repair and drydock facility has recently taken delivery of two Atlas Copco centrifugal compressors to replace smaller screw-type units. This is the first tranche of Atlas Copco units in the eventual transition to a full complement of centrifugal compressors.
"Two Atlas Copco water-cooled discharge compressors were recently installed at Dubai Drydocks, to supply air power for tools, paint removal and ventilation units, making a current total of seven Atlas Copco centrifugal compressors," said Atlas Copco Applied Compressor and Expander Technique, a company within the Atlas Copco Group.
Atlas Copco is an international group of industrial companies with its head office in Stockholm, Sweden. In 2000, it had revenues of $5 billion, with 98 percent of it coming from outside Sweden. Companies in the Group develop, manufacture, and market electric and pneumatic tools, compressed air equipment and generators, construction and mining equipment and assembly systems, and offer related service and equipment rental.
Working in parallel with the existing machines, the compressors each contribute 8,750Nm3/hr of air at 8bar, the company said.
Replacing the older units, the new compressors are housed adjacent to the Drydocks' workshop facilities, in a dedicated building. Either of the water-cooled three-stage compressors can be isolated for maintenance without affecting the system operation.
The two units supply base load on a 24-hour operating basis for air-powered tools, grit blasting and paint removal. They also supply air ventilation for cargo holds and spaces of vessels that are under repair.
The dry-dock facility has a total of five older centrifugal compressors, four housed in an adjacent building and the fifth installed on the floating dock. During the summer peak season, the combined compressor output reaches a yard capacity of 72,000Nm3/hr.
With a total of three 'graving' docks and eight repair berths, as well as a floating dock, the Dubai facility is the Middle East's largest repair yard, and can handle any existing size and type of commercial ship or platform.
As well as repair work, Dubai Drydocks also undertakes some ship conversions and building work. The yard has constructed several with a 50t bollard pull capacity, a suction dredger and workboats. The facility's floating dock, measuring 190m x 34.8m, was the first structure built on-site with a capacity of 15,000t and accommodation for vessels up to 40,000 dwt. Aluminium vessel building facilities have recently been added, and the first aluminium vessel was delivered in January this year.
Today, world-wide customers vary from oil tankers and oil rigs, to merchant vessels and even warships.
Three large dry docks measuring 370m x 66m, 525m x 100m and 415m x 80m respectively contribute to make this the region's most comprehensive maritime repair facility. Despite their size at 12m deep, all of the docks can be dewatered in three hours. The 2,900m of wet berthage, with full craneage cover, are sufficient for eight vessels to undergo repairs prior to or following drydocking.
A total of 10 rail-mounted harbour cranes are installed in the yard, with the three 'graving' docks each covered by a 120t lifting capacity unit.
Dubai Drydocks also has a fully equipped machine and fitting shop which houses an extensive range of machinery, including one of the world's largest ram borers, a 20m shaft lathe and a 20t balancing machine.
The yard also has one of the region's finest electrical repair shops, as well as a steel plate shop and a pipe shop.
A fleet of 52t bollard pull capacity tugs are permanently based at Dubai Drydocks, ensuring that the facility is never short of dock assistance for vessel manoeuvres.
The 2,900m section of wet berthage, with a full craneage cover, is sufficient for eight very large crude carrying (VLCC) vessels to undergo repairs, simultaneously with those in the docks. All repair berths and docks are covered by services such as electric power supply, ballast water, cooling water, fire lines and compressed air supplied by Atlas Copco.