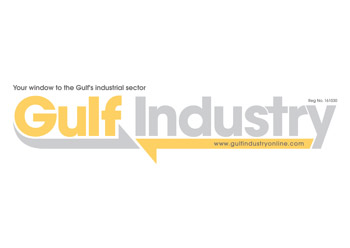

Milliken’s theme for K 2010 of increasing sustainability through additive innovation finds perfect expression in its latest generation of Millad clarifying agents for polypropylene (PP), the company says.
Milliken is already known as one of the world’s leading suppliers of clarifiers that enable polypropylene, one of the most sustainable plastics on the market, to compete for applications demanding excellent optics but normally requiring more costly materials. Now, its new Millad NX8000 series not only sets a new benchmark for clarification but also enables processors to make substantial improvements in their economics through reduced processing temperatures and shorter cycles.
The use of Millad NX8000 in commercial applications has grown substantially in recent months, following its public unveiling at K 2007. “It’s quickly becoming the industry standard,” says Brian Burkhart, global market manager, polypropylene clarifiers. “No other additive puts clarity and gloss levels in PP on a par with other ‘glass clear’ polymers and even glass itself.” It is equally applicable in products made by injection moulding, extrusion blow moulding and injection blow moulding.
The tunable property of Millad NX8000 in random copolymer enables a wide spectrum of solutions ranging from “Ultimate Clarity” – step change in clarity and gloss in polypropylene to levels comparable with “glass clear” polymers and glass – up to “Enhanced Quality” - significant improvements in transparency of PP combined with a wider processing window and improved productivity.
The principal purpose of Millad NX8000 is to enhance optics, but Burkhart says practice has shown that processors can also make considerable energy savings by using the additive. Numerous trials carried out by Milliken have proven that the additive can regularly yield cycle time reductions of as much as 15 per cent, while the ability to process at lower temperatures can often cut energy consumption by 15-20 per cent - and in some extreme cases by over 30 per cent.
An injection moulder normally processing polypropylene at 240-260°C can drop machine settings down to around 200°C if they are using a compound containing Millad NX8000.
![]() |
Milliken has wide-ranging |
“Conventional clarifiers need a certain minimum level of energy input - which typically requires temperatures over 220°C during processing - to ensure full solubility and hence performance in the final application,” says Milliken development engineer Adam Newberry. “Millad NX8000 has much better solubility characteristics in PP, and these allow lower processing temperatures to be used.” In some cases, temperatures can be reduced by as much as 30°C.
“Savings will vary according to the equipment you are running, the process you use and the part you make,” says Burkhart.
Milliken is now launching a version of the additive that is specifically aimed at extrusion blow moulding, Millad NX8500E. “With this new innovative grade, transparency in extrusion blow moulding is no longer limited to PVC or PET,” says Burkhart. Millad NX8500E will allow processors to optimise surface properties as well as bulk haze. It has been designed specifically to provide a step-change in optical properties with standard Ziegler-Natta PP EBM resins. Bottles produced with Millad NX8500E will exhibit excellent gloss and transparency and they will have a fresher look due to a low yellowness index. As with NX8000, improvements are less dependent on processing temperature than with existing clarifiers. Furthermore, no special mould finishes are required to achieve excellent looking bottles.