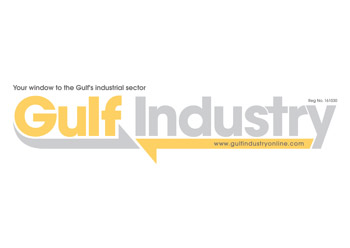

Ingersoll-Rand (IR) Company has introduced in the UAE an advanced rotary air compressor that will enable businesses to reduce their energy consumption and costs by a minimum of 28 per cent during the unit’s operating life.
Known as the Nirvana air compressor, the new IR unit is the first to feature a Hybrid Permanent Magnet (HPM) synchronous motor, an emerging technology that delivers significant customer benefits including increased efficiency and reliability.
“By incorporating the benefits of the HPM motor into an advanced design package, the Nirvana air compressor offers customers the features that they value most – energy-efficiency, increased reliability, lower operational costs and reduced maintenance expenses,” said David Welch, global marketing director of IR’s Air Solutions Group. “The Nirvana air compressor offers a viable and cost-effective solution for customers’ air compression needs and further demonstrates IR’s commitment to design excellence and technological innovation.”
According to the US Department of Energy, industrial air compressors consume 90 billion kWh/year of electricity, which is between 10 and 12 per cent of all industrial energy used in the US. This accounts for more than $4 billion in expenses for businesses and substantial demand on already overburdened public utility grids, resulting in a great market demand for energy-efficient air compressors.
The energy-efficient Nirvana system features fewer rotating parts than any other air compressor in its class. Mounted onto the compressor in a cantilever fashion, the HPM motor directly drives the Nirvana compressor and helps improve reliability by eliminating the need for motor bearings, gears, pulleys, belts, couplings or motor shaft seals.
“With fewer components to wear out, leak or get out of alignment, the Nirvana compressor offers increased reliability and simple maintenance, thus helping customers avoid costly repairs and system failures,” said Ken Schoeneck, global engineering director of IR’s Air Solutions Group. “Coupled with IR’s time-proven, reliable airend, Nirvana is as low-maintenance as an air compressor can get.”
Developed by Leroy Somer, a French division of Emerson Electric, the HPM motor used in IR’s Nirvana system offers increased operating efficiency, easier maintenance, lower costs and a compact design.
Approximately 1/3rd the size of conventional induction motors, the HPM motor is controlled by variable speed inverters which match compressor output to demand at all times. By comparison, typical induction motors operate only at fixed speeds, which wastes a great deal of energy.
In addition, the HPM motor is significantly easier to repair than conventional motors. Instead of complex, continuously wound windings found within the stator of a traditional motor, the HPM motor stator features independent coil modules that can simply be removed and serviced on site by trained IR technicians.
This means that repairs can be completed at a fraction of the cost to rewind a conventional motor and done within four to six hours instead of days or weeks often required for other motors.