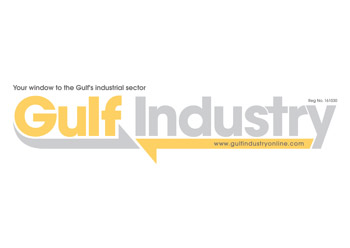

One of the Middle East’s best-known mining companies is set to diversify its operations and engage in value-added activities.
Oman Chromite Company (OCC), whose main business is extracting chromite ore and exporting the ore and chromite powder, will soon participate in the extraction of industrial minerals for the construction industry, general manager Humaid Al Muslmani says. Construction material including aggregates silica and marble will be produced in a joint venture with a local firm.
Al Muslmani also said the company was contemplating upgrading its chrome ore extraction by setting up either a ferrochrome plant or a beneficiation plant near the mining sites. “We’re also thinking in terms of offering blasting services to the market by using our licences and our expertise,” he said.
The company is in the process of installing a new crusher to raise production of chromite powder and augment supplies to overseas markets.
The industrial minerals enterprise has been set up with Oman Cement Company and Al Batina Development and Investment Holding Company. The joint venture, named Al Batina Quarries Company, will produce construction aggregates, marble, silica and limestone, among other things.
“Presently we are in the final stages of preparations to open our first quarry in the Shinas wilayat of northern Oman. The deposit is estimated to have a reserve of about 300 million tonnes of gabbro rocks,” said Al Muslmani. The quarry, which will begin operations next year, aims to produce two million tonnes per year of various types of aggregates.
OCC produces chrome ore of refractory and metallurgical grades from mining in the wilayats of Liwa and Shinas. Production of the refractory grade was 7,804 tonnes in 2002, but exports were 8,081 tonnes. This was possible because of accumulated stocks from previous years.
Production of the same grade in first-half 2003 was 5,220 tonnes and exports were 3,428 tonnes. Production for the whole of this year is expected to reach 15,000 tonnes.
The company produced 19,640 tonnes of metallurgical-grade ore in 2002, up 7,290 tonnes over the previous year. However, there was no production of that grade in the first half of this year, nor will there be any produced for the rest of the year. There were no exports of the grade in 2001, 2002 and the first half of this year, leaving large quantities in stock. According to the company, stocks had been held because prices were too low, but with prices picking up in the second half, some shipments have commenced.
Chromium’s refractory uses include magnesite-chrome firebrick for metallurgical furnace linings and granular chromite for various other heat-resistant applications.
In the metallurgical industry, chromium is an important component of stainless steels and various metal alloys. Metal joint prostheses made of chromium alloys are widely used in clinical orthopaedics.
The chemical industry uses chromium primarily in paint pigments (chromium compounds can be red, yellow, orange, and green), chrome plating and leather
In Oman, Chromite was discovered in 1971 during exploration for other minerals, and systematic prospecting for the ore started in 1974, revealing 300 occurences in two areas in the country’s northern part. The total reserves of chromite are estimated to be more than two million tonnes.
The Omani government has a 15 per cent stake in OCC while Oman Mining Company, Police Pension Funds and Al Qurm Establishment each have a 10 per cent share. Public shareholders hold the remaining 55 per cent stock.
Exports are conducted through traders. China has been the main buyer of metallurgical-grade ore, while Japan, the UK, Germany, Thailand, South Africa and Spain have imported the company’s refractory grade.
OCC’s chromite powder is mainly obtained from the refractory grade and exported to Japan, South Korea, and Thailand. In the past few years, the company established new markets in the UK, Germany and Spain and is trying to open up further to other European markets. The company exports limited quantities to South Africa.
Production of chromite powder and chips goes up to 5,000 tonnes annually, but a new crusher will raise that level to 7,000 tonnes when it is put to use alongside the main crusher next year.
The company is gauging the market prior to deciding whether to set up a ferrochrome plant. Ferrochrome, one of the two forms of chromium, the other being the pure metal itself, is a carbon-containing alloy used to manufacture hard ‘chromium’ steel. Ferrochrome is formed when a mixture of chromite, coke and limestone is heated in a furnace.
“The main concept would be to upgrade the metallurgical-grade ore and raise the chromium content from 38 per cent to 58 per cent,” said production manager Obaid Al Sulaitni. “The beneficiation plant would be viable only if it assures high-purity chrome ore.”