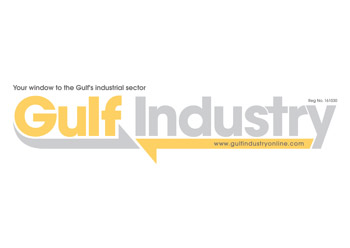

When an Indian migrant came to Oman in 1979 with thoughts of a business career, he did not have far to look.
All around him was mountainous terrain with the promise of abundant raw material to start a building products industry. Koshy P Thomas decided he could capitalise on the silica, sand and marble reserves by devising a formula to produce architectural stone slabs that would look as natural as anyone could possibly make them. After much trying and testing, Thomas emerged with a product he would call Decorstone and which could be used for external and internal cladding while being strong enough to last a lifetime.
Commercial production of Decorstone commenced at the Rusayl Industrial Estate, near Muscat city, in 1986. Over the years, Decorstone International LLC has produced enough veneer material to clad more than 5,000 villas and commercial buildings including many abroad and some belonging to government organisations. Along the way Thomas also won international recognition in the form of the Grand Prix European Award for quality and prestige. Decorstone has set up a subsidiary in Sharjah in the name of Creative Stone and “sold” its technology to two US companies, one in Seattle and the other in Denver.
This year the company introduced what it describes as an upgraded formula. “We have revised the mix in a different proportion and with special additives to give extra strength and better adhesion,” said Thomas who presents himself as the inventor of Decorstone. The slabs will also be bigger in size, going up to 500mm x 300mm against the previous maximum of 340mm x 150mm.
According to the company, Decorstone is prepared from a judicial mix of rock powder, silica, lightweight sand, perlite, white cement, ordinary Portland cement, marble chips, iron oxide, pigments, decobul (a concentrate prepared by the company for injection into the mix to give the stone its light weight and insulation) and other additives. The perlite comes from Cyprus and the iron oxide from Germany. The raw materials are fed into a reactor and mixed. Additives are injected at high pressure forming millions of microbubbles that make the stones lightweight and grant them good insulation properties.
“There’s no room for inaccuracies because product quality depends largely on its specific composition,” says Thomas. The light weight of the stone makes installation easy and Decorstone can be applied over dry walls, brick, stucco, wood, celotex, concrete and almost any surface, he explains.
The company has outlined installation procedures that labourers have to follow. Mortar has to be applied to the reverse before fixing firmly against the wall. The stone can be applied to any structurally sound masonry surface. Smooth or pointed concrete surfaces should be thoroughly hacked or chipped. When installing the stone in straight courses, the line of application should be straight and level. Joints of approximately 10mm width are left between each stone and can be grouted with contrast colour or similar colour. All surfaces, which are to receive the stone, have to be thoroughly soaked with water prior to application. Curing has to be carried out in the same manner as in sand and cement.
“Once you fix it, you can simply forget it. No further maintenance is necessary. The colour and appeal is permanent. It is attractive, versatile, has a total absence of efflorescence and reduces the load on the structure of the building,” says Thomas.
The company stresses that the product conforms to British and American standards, has a tensile strength of 3.9n/sq mm and a water absorption level of 10 to 11 per cent, is suitable for all weather conditions and comes in a variety of colours, all of which are permanent. Among the advantages cited are strength, safety, insulation properties, resistance to fire and chemicals and not having to be subjected to maintenance. Tests are done in an independent laboratory and the company makes available its latest technical data on request. The US standard ASTM is used for transmission loss, sound transmission class, thermal conductivity, splitting tensile and compression. For water absorption, the company uses ASTM and BS.
“Decorstone is probably the simplest, most versatile and attractive facing material available in the market today,” exults Thomas. “Increasing labour costs and diminishing natural stone as well as consumer acceptance of manufactured stone have made it a worthy and affordable alternative to natural stone. It has become an integral part of many homes. No matter how it is used, it conveys quality, elegance, stability and tradition. It was created for the express purpose of supplying the building industry with pre-cast stone of unmatched quality.”
Decorstone International LLC functions under the sponsorship of Yousuf Saeed Khamis Al Zadjali with Thomas officiating as managing director.
“Having transferred our technology to the US and set up a successful operation in Sharjah, we’re seeking to make our technology available to interested investors around the world,” says Thomas. “Our plants are available in stationary and semi-mobile formats and our experienced technical staff will be pleased to prepare individual plans for the special needs of our customers.”
An example of a start-up operation, he says, would be a plant with an operational capacity of approximately 1,000sq ft of stone per shift. Production could be increased anytime according to market conditions. “There’s no need for an expensive state-of-the-art manufacturing plant for a start-up. The building should contain a minimum of 750sq m of floor space for production, clean water supply, three-phase electricity and proper drainage. A minimum labour force of 10 is necessary to begin with,” he advises. “With nearly 100 per cent local raw materials, our factories have proved to be economical, reliable and energy-efficient in their operations over the years.”
Decorstone offers a basket of services including market surveys and feasibility studies, the plant layout, supply and installation of equipment, transfer of technology and training. The company promises to organise the start of production on the franchisee’s site and provide geographical exclusiveness for the licence.
Prospects for overseas partnerships seem better than ever before, with Decorstone having gained maturity in its manufacturing process and received substantial purchase orders. Thomas says the company is discussing joint ventures with business promoters in the Indian states of Rajasthan, Kerala and Tamil Nadu. The company’s dream is to establish franchises worldwide.
At its Rusayl plant, the company has been producing at the rate of 2,500sq ft per day, a 20 per cent improvement over last year’s level. This year could see a similar increase in production. Some 35 per cent of the output goes overseas, mostly to the Gulf states. The company has also found buyers in Africa, mainly Djibouti. The UAE takes in most of Rusayl’s overseas consignments.
Decorstone will most likely be in for an expansion with demand set to grow. Expansion would imply setting up a brand new plant in Rusayl.
The Sharjah plant’s operations are on a lower scale, but with the ongoing boom in the construction industry, it expects to produce more in course of time and capture a bigger share of cladding orders. Forty per cent of the Sharjah output is shipped overseas to Iran and the former Soviet states, among other markets.
Decorstone has adorned some prominent structures including the monument at Al Muwalla roundabout near Muscat, the Vocational Centre of Oman’s Ministry of Social Affairs and Labour, several beautification structures of the Omani government, the general secretariat of the UAE municipalities in Abu Dhabi, buildings of the Sharjah Co-operative Society and UAE social housing units.