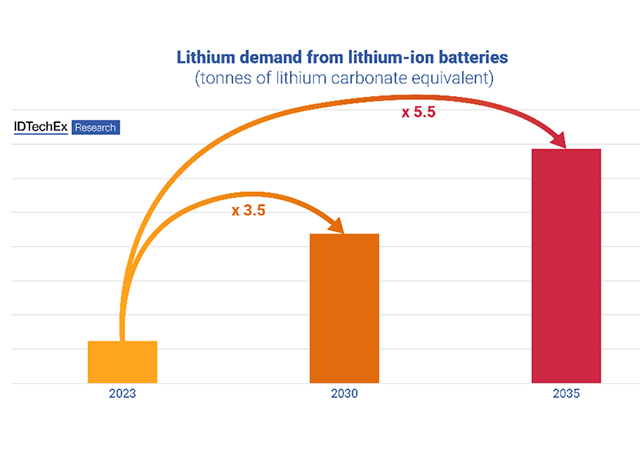
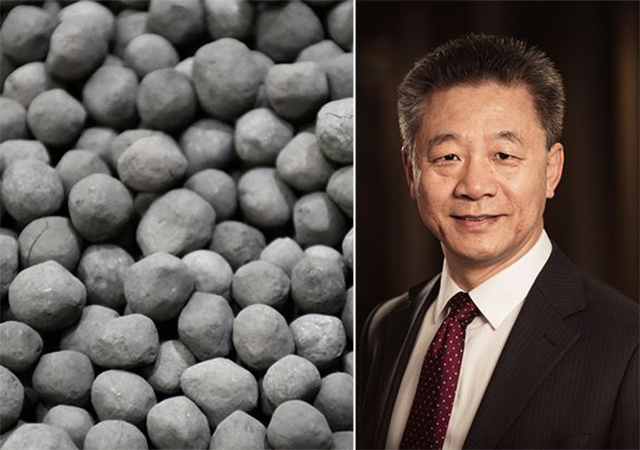
The HYBRIT initiative, a collaboration between SSAB, LKAB, and Vattenfall, has made significant strides over the past six years towards revolutionising the iron and steel industry.
Launched in 2016, this project aims to virtually eliminate carbon dioxide emissions from steel production by replacing traditional fossil fuels with fossil-free hydrogen and electricity.
The results of this extensive research have recently been compiled in a final report presented to the Swedish Energy Agency, showcasing the feasibility of producing fossil-free iron on an industrial scale.
ACHIEVEMENTS OF THE HYBRIT INITIATIVE
The final report highlights that direct reduced iron (DRI) produced using the HYBRIT process demonstrates superior characteristics compared to iron produced with fossil fuels. This innovative process is poised to significantly reduce Sweden's carbon dioxide emissions by over 10 per cent and Finland's by around 7 per cent. The initiative has also secured multiple patents based on its successful findings, signaling a promising future for fossil-free steel production.
TRANSFORMATIVE IMPACT ON THE INDUSTRY
Martin Pei, Chief Technology Officer at SSAB and Chairman of Hybrit Development AB, expressed immense pride in the initiative’s accomplishments. “Thanks to the successful results of the pilot project, we are well on our way to fundamentally changing the iron and steel industry,” he stated. SSAB has already begun investing heavily in converting its Nordic production system to fossil-free steel, with initial deliveries of fossil-free steel to customers in various sectors, including automotive and construction.
A UNIQUE VALUE CHAIN
HYBRIT's process represents the first successful demonstration of a fossil-free value chain for iron and steel production at a semi-industrial scale. Over 5,000 tonnes of hydrogen-reduced iron have been produced at the pilot plant in Luleå. Major companies such as Volvo Group, Epiroc, and Peab are already integrating this fossil-free steel into their products, highlighting the growing interest and demand for sustainable materials.
RESEARCH OUTCOMES FROM 2018 TO 2024
The research conducted from 2018 to 2024 focused on scaling up technical solutions from the laboratory to industrial applications. Key achievements include:
Development of Hydrogen-Based Technology: The initiative has developed an innovative technology for efficient fossil-free iron and steel production, achieving an impressive 0.0 tonnes of CO2 emissions per tonne of steel produced.
Introduction of Sponge Iron: A new product, sponge iron, has been created with significantly improved properties compared to iron reduced using fossil fuels. This carbon-free iron boasts a high metalisation degree (98-99 per cent) and enhanced resistance to mechanical stress, making it more suitable for transport and storage.
Long-term Operation of Electrolysers: The project successfully operated alkaline electrolysers for hydrogen production and storage, demonstrating the potential to reduce hydrogen production costs by up to 40 per cent through real-time market testing.
Efficient Melting Process: A collaboration with Swerim research institute has resulted in an effective process for melting sponge iron into crude steel in electric arc furnaces, producing steel of comparable quality to traditional methods.
NEXT STEPS: SCALING UP FOR INDUSTRIAL PRODUCTION
Having completed the pilot phase, the HYBRIT initiative is now transitioning into its next phase, focusing on the industrial-scale implementation of its technology. Hybrit Development AB will continue to conduct research and development in partnership with the owner companies, supporting LKAB's planned demonstration plant in Gällivare, which will be a crucial step towards full-scale production.
Jenny Greberg, Vice President of Technology at LKAB, expressed optimism about the project's future, stating, “Our high-quality iron ore combined with good access to fossil-free energy provides unique conditions for establishing a competitive value chain for future fossil-free iron and steel production.”
COLLABORATIVE EFFORTS
The success of HYBRIT can be attributed to the collaborative efforts of its partners. Andreas Regnell, Head of Strategic Development at Vattenfall, emphasised the importance of partnership in achieving these results, stating, “The next step is to scale up to an industrial scale where fossil-free electricity and hydrogen enable the transition to a future where it is possible for everyone to transport, produce and live fossil-free.”
FUNDING AND SUPPORT
The HYBRIT project has received funding from the EU Innovation Fund and the Swedish Industriklivet program. It is also part of the European IPCEI project Hy2Use, which encompasses 35 projects across 12 countries aimed at accelerating the transition to hydrogen-based industries.
Klara Helstad, Head of the Sustainable Industry Unit at the Swedish Energy Agency, noted, “The path towards net-zero emissions in industry requires investment in innovative and technology-shifting solutions. The ambition is that the knowledge from the various initiatives will spread and accelerate the industry's transition.”
FUTURE PROSPECTS
The results from the HYBRIT project demonstrate a clear path towards a sustainable future in the iron and steel industry. With the development of efficient, fossil-free processes and products, the initiative not only paves the way for significant reductions in carbon emissions but also sets a precedent for other industries seeking to transition to greener practices.
As HYBRIT moves forward, the focus will remain on refining the technology and scaling it for broad industrial application. By continuing to innovate and collaborate, the initiative aims to establish a global benchmark for sustainable steel production, ultimately contributing to a fossil-free future for all.