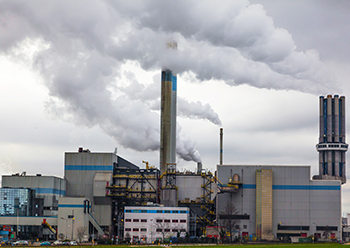
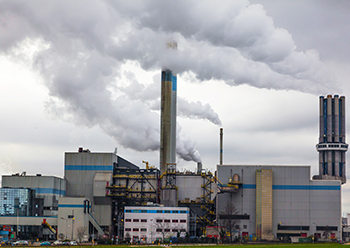
Decarbonising heavy industries and the manufacutring sector - the hard to abate industries - requires support and collaboration of governments and industrial players, introduction of innovative technologies and above all, the willingness of market forces to make the necessary changes.
The efforts required will be similar to that led to the cost reduction and scale up of renewable energy generation, say experts.
Manufacturing is essential for economic growth, and its supply chains are pivotal for ensuring the wellbeing and advancement of people and economies. Among the largest and most critical manufacturing industries are steel, cement, glass, and chemicals.
These industries are the biggest industrial consumers of energy, helping to make heavy industry responsible for 20 percent of global direct carbon dioxide emissions today, says an International Finance Corporation (IFC) report, Strengthening Sustainability Decarbonizing Manufacturing Industries.
Given the integral role that these industries play in the global economy and in people’s lives, it will be critical for them to decarbonise their production processes if the world is to meet emissions-reduction goals and prevent intensifying climate disasters, it points out.
Clearly, decarbonising heavy industries will take decades of work, trillions in investments for capital and operational expenses, and global coordination. Besides adequate supplies of renewable energy, countries and companies, particularly in developing markets, will need support for capital expenditures to retool production, it says.
The steel, cement, glass, and chemicals industries have all been growing exponentially to keep up with the world’s increasing population and the associated demand for building and infrastructure materials. Global demand for steel -- the world’s most traded commodity after oil -- has increased by a factor of three since 1971. Today, steel manufacturers use 8 percent of the world’s energy, mostly coal, and emit 6 to 7 percent of the world’s greenhouse gases.
Cement production, meanwhile, has tripled from just 1995, and now generates about 7 percent of the world’s total emissions, while global sales for chemicals have increased 2.4 times over the last two decades, with the industry accounting for about 5 to 6 percent of the world’s emissions.
Global consumption of glass is forecast to grow by a compounded annual rate of 3.5 percent between 2019 and 2027, driven by both traditional uses and the material’s incorporation into new technologies, including renewable energy systems. While the glass industry only generates 0.3 percent of worldwide CO2 emissions, the energy intensity of glass production surpasses that of cement. The production process also emits combustion byproducts that contribute to climate change.
McKinsey & Company has identified steel, cement, and two subsectors of the chemicals industry (specifically, ammonia, used to make fertilizer, and ethylene, used in many industrial production chains), as the manufacturing sectors emitting the most CO2. McKinsey estimated in a report in 2018 that it would cost over $21 trillion through 2050 just to decarbonise these sectors.
Despite the costs and technical complexities involved, growing global concerns over climate change are putting an increasing focus on sustainability.
Strengthening Sustainability
The steel, cement, glass, and chemicals industries have all been growing exponentially. In decarbonising these industries, the private sector together with governments and a range of other stakeholders are pursuing carbon-abatement strategies to make manufacturing more energy efficient and less harmful to the planet, notes the IFC report.
These strategies involve 1) shifting manufacturers to cleaner energy sources; 2) encouraging more efficient production processes; 3) offsetting the financial costs and risks of decarbonising; and 4) investing in technologies that can eliminate waste by capturing, recycling, remanufacturing, and reusing spent material.
Oil, gas, and coal remain the principal energy sources for manufacturers operating in a wide range of sectors, including steel, cement, glass, and chemicals. This has helped to make these industries among the most difficult to decarbonise. The production of steel, cement, and glass all require extremely high temperatures and thus large amounts of fossil fuels.
Global regulation will also be key. For example, because steel is traded globally, regulating emissions unevenly could shift production to areas where costs are lower and emission standards -- if they even exist - are lax or unregulated.
Sustainability
Manufacturers over the last few decades have substantially improved their energy efficiency and reduced emissions per output. In the steel industry, a growing number of producers are switching to Direct Reduced Iron (DRI) and electric arc furnaces (EAF). These methods rely on natural gas and electricity and use DRI, scrap steel, or their combination, to make steel, resulting in lower emissions and energy-intensity production. In the United States, two-thirds of steel production involves recycled steel from electric arc furnaces.
The cement industry uses waste as a fuel, and substitutes clinker with industrial waste, such as fly ash from power-generation plants; the glass industry has increased its use of cullet, which is made from crushed glass and requires approximately 40 percent less energy than when using raw materials. The chemical industry has secured reductions through process and energy improvements, but it faces a unique challenge, since half of its products use carbon, such as from crude oil, for feedstock.
However, process improvements and equipment retrofits alone won’t achieve the deep cuts that are required for heavy industries to meet the goals set under the Paris Agreement. To guide further reforms, the steel, cement, glass, and chemical industries have drawn up their own roadmaps for achieving net zero by 2050.
Many of the innovative technologies needed to achieve these goals already exist, and some are being piloted. In the steel sector, the Al Reyadah Carbon Capture, Use, and Storage Project in the United Arab Emirates is capturing CO2 from the flue gas of an Emirates Steel production facility and injecting it to conduct enhanced oil recovery in the Abu Dhabi National Oil Company’s oil fields nearby. The project includes capture, transport, and injection of up to 800,000 tons of CO2 annually and is part of a bigger potential plan to create a CO2 hub to manage carbon dioxide supply and injection requirements in the UAE, notes the report.
The cement sector is also exploring the use of carbon capture, use, and storage, with the LEILAC 2 project testing the technology at HeidelbergCement’s plant in Hanover, Germany, with a slated 2023 operational date. To roll out these cutting-edge solutions at scale, however, will require huge capital investments at attractive commercial terms as well as additional research and development for heavy industry to decarbonise coupled with a supportive ecosystem.
Challenges & Opportunities
Coal makes up 75 percent of the fuel used to produce iron and steel, and 60 percent of the fuel used to make cement. Natural gas and oil are the dominant fuels used in the manufacturing of petrochemicals. Finding substitutes for old fossil fuel-powered blast furnaces and factories is a significant challenge. Old equipment is expensive to replace, and it’s difficult to find enough renewable capacity capable of generating industrial-grade heat on a 24/7 basis.
Various strategies can drive behavioral change among companies and their consumers and investors. Governments and other stakeholders including the International Finance Corporation (IFC) are working with the private sector on a range of such strategies to help manufacturers in heavy industries achieve greener production -- plus financial savings and a competitive edge.
Shifting to Cleaner Energy
Capacity for wind and solar power is growing, and policies announced by the US and EU in 2022 should accelerate this trend. The International Energy Agency estimates that renewable’s share must double from 30 percent in 2021 to more than 60 percent by 2030 to meet the green energy needs required for the world to achieve net zero by 2050.
Heavy industries will require four to nine times as much clean energy to decarbonise, compared to the status quo. Using biocarbons as replacement fuel or feedstock in some heavy manufacturing provides another way to reduce emissions. This change typically could be implemented without expensive retrofits to blast furnaces; the challenge is finding enough sustainably produced biofuels. And biofuels still emit CO2, though their net emissions are lower.
Green hydrogen offers one of the most promising long-term solutions. Hydrogen exists in abundance in nature and is used in some production processes including for feedstock. It also has the potential to power manufacturing processes and to store and transport energy. But production of carbon-neutral hydrogen requires renewable power -- and enough of it -- to break apart hydrogen’s bonds and release energy through electrolysis.
Hydrogen is also used in other ways in the production process, including as a lower emission reduction agent in steel production. Used to make ammonia, green hydrogen could help to decarbonise the agricultural food supply chain.
Improving Efficiency
Trillions of dollars of investment will be required to phase out the thousands of existing coalcombusting steel, cement, and chemical plants around the world that are responsible for most industrial emissions. Investing in more efficient production offers one of the fastest ways to reduce manufacturers’ carbon footprint, while also boosting their bottom line through reduced energy and raw material use.
A wide range of options for improving efficiency is available to hard-to-abate industries, and IFC can advise companies on what works best for them.
IFC supports a number of strategies aimed at decarbonising heavy industries, with a focus on promoting energy efficiency, renewable and alternative energy, emerging technologies, and resource efficiency.
Construction Materials (Cement, Steel, Glass): Potential energy-related strategies include adopting modern kiln technology and vertical roller mills (for cement); optimising blast furnace operations (steel); upgrading furnaces such as by installing waste-heat boilers (glass); and employing electric arc furnaces (steel and glass).
The three industries could employ waste-heat recovery and power cogeneration systems, adopt solar and wind power, and incorporate biomass or biogas as alternative reductants or fuels. Emerging technologies that could help all three industries include green hydrogen and CCUS, while the cement industry could also increase its use of blended and green cement.
To improve resource efficiency, industries could alter designs to lightweight products or change the production process (such as using the narrow neck press and blow approach to produce glass bottles), saving on raw materials and energy. They could increase the use of recycled content, including recycled concrete, cullet or waste glass, and scrap steel.
Offsetting Costs and Risks
Governments can help offset the costs and risks of decarbonisation by providing tax breaks and subsidies for businesses that shrink their carbon footprint. Regulations can also help to make the enabling environment more conducive to decarbonisation, such as through cap-and-trade programmes. Policy makers can assist in creating a supportive ecosystem through such measures as clean energy standards and investment in infrastructure supporting recycling and reuse.
Meanwhile, development organisations such as IFC can help mitigate the financial risk by extending risk-sharing lending arrangements or by anchoring investments.
In the longer term, decarbonising operations can help manufacturers maintain their competitive edge. Companies are not only facing growing pressure to become more sustainable from consumers, investors, and corporate boards, but must also consider how best to protect their operations from a changing climate and potential future shortages in essential inputs, from water to rare earth minerals.
Investing in Technology
Technologies are capable of eliminating waste by capturing, recycling, remanufacturing, and reusing spent material. One proven method for limiting CO2 emissions is carbon capture, utilization, and storage (CCUS), with the gas then stored or used for other purposes.
Widespread adoption will depend in part on the economic viability of sequestering carbon.
Currently, technologies are in the early stage, with years of development needed before they become commercially viable. Broad use of CCUS will also require the development of transportation and storage infrastructure. Another decarbonising strategy is to simply reduce demand for certain manufactured products. Significant research and development is going into finding more sustainably manufactured products such as building materials that can replace steel, cement, and glass.