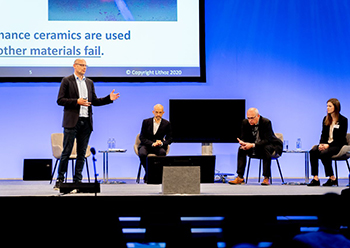
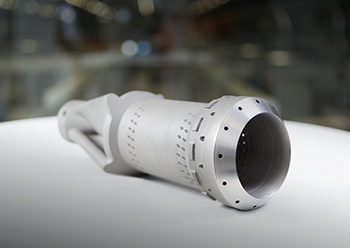
DNV and Siemens Energy's global additive manufacturing business unit are joining forces to create a quality assurance platform for the additive manufacturing (AM) – also known as 3D-printing – industry.
The collaboration will accelerate commercial AM production with quality control at every stage and layer in the printing process, the two companies said.
Siemens Energy's experts in Finspång, Sweden, have developed the first generation of the AM Cockpit platform providing automated, reliable quality control of the 3D metal printing process. In turn, DNV has developed the Independent Quality Monitor (IQM) platform – a customer portal that continuously quality-assures digital solutions.
By combining these two solutions, DNV can launch a commercial solution for the AM manufacturing industry – ensuring that 3D-printed parts can easily be compared to a so-called approved master print. The combination also makes automated and remote process certification possible
Successful combination of two platforms
The AM Cockpit collects sensor data streams and powder bed images from the manufacturing process in powder bed fusion 3D-printers. The AM Cockpit then generates a digital summary of each printed part, highlighting problematic areas of the print.
In parallel, the IQM has been developed as part of the EU-project InterQ (https://interq-project.eu/), aiming at zero-defect manufacturing. The solution monitors data quality continuously through newly developed algorithms and compliance logic.
"Succeeding in AM industrialisation relies on a successful digital transition. The combination of the AM Cockpit and the IQM is a significant step forward for additive manufacturing," says Klas Bendrik, Chief digital and development officer at DNV.
By industrialising the combined solution, DNV aims to become the global energy sector's preferred choice for digital risk management.
Senior engineer and AM specialist Stian Gurrik have been central in working with DNV's recommended practices on additive manufacturing. He sees several benefits of the collaboration between DNV and Siemens Energy.
"The benefits of 3D-printing, when used properly, can include reduced material waste, quicker production, cost savings and the ability to produce complex and customized parts," Gurrik says.
Enabling industry decarbonisation
Siemens Energy is leading the way in the energy transition – covering the entire spectrum of energy solutions and supporting its customers' ambitious decarbonisation targets.
As a pioneer in AM, Siemens Energy has been a global front-runner in designing and 3D-printing key gas turbine components that enable power plant owners to increase their plant's efficiency and significantly reduce carbon emissions today.
"Thanks to its design freedom, AM is the core technology that allows Siemens Energy to develop and modify gas turbines to run on green fuels, such as hydrogen," says Hans Holmström, CEO of Siemens Energy in Sweden.
"With decades of experience in industrializing additive manufacturing, Siemens Energy is an excellent partner for DNV in advancing quality assurance of additively manufactured parts," says Manish Kumar, Head of business development, strategy and sales of Siemens Energy Additive Manufacturing Business.
The quality of a printing process can be visualised with the digitalised quality assurance method of the AM Cockpit and the IQM. As a result, the end user can be confident that the process meets the necessary quality standards.