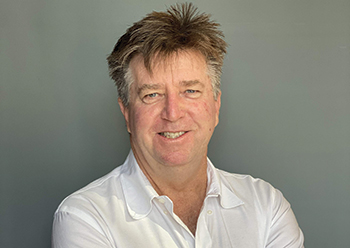
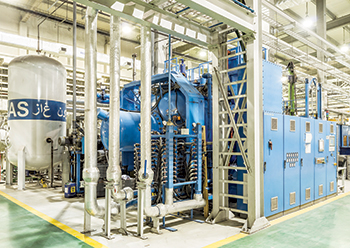
Manufacturers are no strangers to dealing with turbulent market conditions, however the current global landscape is a sea of uncertainty that can sink even the most buoyant of companies.
That said, new technologies, improved planning and better use of data have created huge opportunities for companies to adapt and become more resilient.
In this year’s Manufacturing trends and predictions, IFS’s Global Industry Directors – Manufacturing, Maggie Slowik and Andrew Burton have come together to analyse key market insights that point to five unique predictions that outline how manufacturers can become more resilient in this new normal.
Prediction 1: By 2024, ESG Governance will have shaped the extent to which 70 per cent of manufacturers are tracking their ESG scope 1 and 2 emissions using digital technology and improving the accuracy of their scope 3 metrics.
ESG, as a measurement of a company's environmental, social, and governance initiatives, has become an essential component of how organisations are assessed and valued — by investors, partners, customers, and employees alike.
For manufacturers, the primary focus at present is on the environmental, or `E’ aspect of ESG, with the ultimate mandate to show progress towards decarbonisation. Back in January 2022 we predicted that 75 per cent of manufacturers would prioritise decarbonisation as part of their sustainability efforts.
Manufacturers voluntarily comply with reporting even when this means dealing with a complex set of reporting regulations, ratings, and disclosure frameworks. In a recent IFS Sustainability focused customer day, attendees indicated that they typically adhere to 3 main reporting standards and frameworks: the Global Reporting Initiative (GRI), the EU’s Corporate Sustainability Reporting Directive (CSRD), and the CDP Climate Change Programme. We also see commitment to the Science-Based Target Initiative, and the Corporate Net-Zero Standard.
The ESG landscape is ever evolving, and we are already seeing regulatory frameworks emerging to standardise the reporting and disclosure of ESG metrics around the world and jurisdictions
For instance, the EU as part of its Green New Deal program for a low-carbon economy, has adopted the Corporate Sustainability Reporting Directive (CSRD), where metrics are specified under the European Sustainability Reporting Standards (ESRS) which has been submitted to the European Commission.
However, at present we see most manufacturers lacking the capabilities to track scope 1, 2 and 3 emissions. This is mostly due to the fact they are still manually collecting these metrics from within their organisation across entities and different systems while using Excel as a repository and analysis tool.
2023 will see manufacturers investing in technology in earnest, to help automate and ingest consistent, comparable, and reliable carbon metrics as part of their enhanced ESG disclosures.
While this will be easier for scope 1 and scope 2 emissions, which are from emission sources owned and controlled by organisations, scope 3 emissions will remain a challenge for most, but will not be lesser of a priority. Here’s why:
Scope 3 emissions (all the emissions indirectly generated by a business) account for the largest share of most companies’ greenhouse gas (GHG) emissions, this can account for up to 75 per cent of companies’ greenhouse gas emissions on average, and therefore representing a large proportion of climate-related risk.
Prediction 2: By 2024, over high proportion of manufacturers will appoint resources to roles in digital science to support the development of their digital twin strategy.
As the integration of applications and machines progress the amount of data being collected is increasing exponentially.
It is estimated that there will be 41.6 billion devices connected to the internet by 2025. 127 new devices are connected to the internet every second which will lead to 79.4 Zettabytes of data by 2025. (Source IDC)
Not all these new connected machines are being used in manufacturing. However, it does show that machines and devices being connected to the internet and each other will be generating huge amounts of data. This data must be understood, controlled, managed, and checked for accuracy as this data will form the basis of real time decision making. This will need new skills that are not currently employed in many manufacturing companies.
Manufacturers are realising the importance of their data, and how it is, or will run their decision making in real time.
New positions are being created for Data scientists, or Chief data officers, whose role is to understand the data and how it is used. They will be responsible for the accuracy of the data and to understand where the data is coming from and its impact on the day to day running of the business.
Manufacturers who include this role will be able to move through the data transformation journey and harness the power of digital twin in their business than those who do not.
Prediction 3: Increased macroeconomic turbulence, will see 60 per cent of manufacturers scale up digital investments beyond pilot purgatory to drive business value.
Global supply chain shortages, price inflation and recession, are increasingly pointing to digitalisation as an enabler for companies to withstand geopolitical and macroeconomic disruptions.
But the question remains, digitalisation is not new and so to what extend have manufactures been able to make use of their technologies to protect their business performance? We have seen the basics covered: reduce costs, improved operational efficiency and shortened time to market are amongst the main benefits, but have manufacturers really made the most of their digital transformation investments?
In a recent IFS / IDC we asked manufacturers to self-assess their digital maturity. The Study found that 75 per cent consider themselves as digitally mature. A study by McKinsey highlights that many manufacturers have not been able to move beyond “pilot purgatory”, meaning that they have not been able to scale successful pilots programs or fully leverage new tools and technology to see meaningful returns/business outcomes. The differences between the two study points a shortfall in devising a true long term and business wide vision on the value digital transformation can bring.
The widespread toe-dipping pilots have created a ‘try before we buy’ mentality and has isolated digital technology away from Business as usual. Other reasons include lack of leadership and strategy, siloed implementation, and a technology-first (vs business first) approach. These findings are compounded by findings that 62 per cent of manufacturers are struggling to articulate digital technology ROI which if deployed in siloes is to be expected.
2023 is the continuation of unpredictable market dynamics and manufacturers must start re-evaluating their digital transformation strategies to prevent further depletion of their investments and efforts. This will require focusing on real business needs, use cases and challenges, and integrating pilots into their mainstream business processes and rolled these out across the wider manufacturing network.
The additional drawback of pilots is the impact this has on talent. Digital skills remain locked away and to realise the full value of their digital transformation manufacturers must also focus on accelerating their people enablement plans when it comes to digital skills. Without this, projects will likely need to be postponed will be slower to deliver ROI and lose the support of executives. As well as building up internal skills, manufacturers need to attract, build and retain digital skills from industries that have been faster at transforming and help them create a competitive advantage.
The IFS/IDC study also showed that digital transformation, if successfully envisioned and executed, has a strong impact on an organisation’s revenue and profit performance. It’s time to get into the details by re-setting the focus on business, not technology, first!
Prediction 4: By 2025, 2 out of 3 manufacturers will have digitally enhanced their legacy assets enabling them to be connected to their MES systems to improve productivity.
New production machinery is considerably easier to connect to business systems; Manufacturers who have been able to invest in modern machinery and connect them to their business enterprise systems are seeing impressive results that are impacting business performance.
However, not all manufacturers are in this fortunate situation and many still own large expensive production machinery, built before the computer integration came as standard. These manufacturing companies’ risk being left behind those that are along their way on the digital transformation journey unless they take action to modernise their operations and integrate their assets into their broader system by adding sensors throughout and achieve real time visibility of the asset’s performance as well as take advantage of predictive maintenance capabilities.
This asset modernisation approach is more cost effective in a lot of cases as capex investments are not required and the ramp up to digital transformation can be made smoother without compromising on value delivered. The increased demand for sensors for legacy machinery points to a renewed focus on MES roll-out in the next couple of years.
Prediction 5: By 2025 – 40 per cent of manufacturers will use AI to bolster business decision making.
As manufacturers continue their digital transformation journeys the amount of data that is now available has increased exponentially – a contributing to this journey and aiding the interpretation of this data is Artificial Intelligence (AI) – what was once only conceived as cinema fiction has become a modern-day reality for many manufacturers.
Beyond the physical world of robotics, drones and autonomous vehicles, it is what we can’t see that is really changing and influencing manufacturers globally to think and act differently. AI and machine learning are allowing manufacturers to make smarter, more accurate and actionable decisions – essentially enabling a standard production line, to become more autonomous as each moving part can think independently and acts on future information like weather forecasts and consumer spending habits. It’s this smart way of thinking that is allowing manufacturers to become leaner and more agile – and crucially home in on their customer centricity strategy.
The scale of AI growth is clear to see, with it being reported that by 2027 the AI market will be worth 16.3 Billion US dollars, this growth will likely lead to 40 per cent of manufacturers using AI to contribute to crucial decision-making processes, but our experts feel this is really just the tip of the iceberg, AI will go much deeper than that and will include vastly improving factories efficiency, training staff and meeting sustainability goals.
For many that are on the AI journey benefits are already visible; for those that are just starting out it can be a daunting task knowing where to begin, with questions such as do you make your legacy factory smart, do you add sensors to warehouses or look at using algorithms to predict consumer habits? There may be an opportunity to first consider AI to help guide the decision.
NAVIGATING THE UNKNOWN
Process or discrete manufacturers, or a hybrid of both, are being forced to rethink how they operate. The reality is that the current levels of uncertainty created by geopolitical events, supply chain disruptions locally and globally and the ensuing reactive consumer behaviour are not making this a question of “if” but “when”.
A clear certainty is that resilience, agility and adaptability are technology dependent to allow companies to stay preforming relevant and profitable.