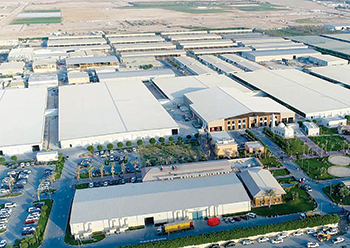
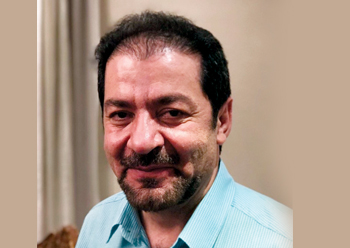
Decanter centrifuges are currently the preferred and most popular equipment used for thickening and dewatering the sludges produced in water treatment and wastewater treatment plants. Decanters were introduced into the wastewater treatment process seven decades ago and utilization has accelerated considerably in the last 20 years, in parallel with the development of automation technology.
Decanters are now, in addition to processing sludge in an efficient way, provide more uptime, reliability, and peace of mind to plant operators thanks to highly skilled PLC-based automation systems. However, market expectation is increasing beyond these.
Automatic regulation of the critical decanter parameters with a PLC is the basis for continuous, constant and safe operation for most decanters but is not the only feature able to increase the lifetime of the equipment and further reduce operational costs such as polymer supply, maintenance work and disposal of the cake. To be able to meet today’s expectations, extra features can be added to the automation scope of the decanter.
![]() |
Decanter Test Centre |
Centrifugal decanters are manufactured globally for different markets, alongside the continuous development of automation platforms for products. The result of a long R&D journey, recently launched services serve as part of IoT solutions to decanter customers.
Connected services focus on maximizing process performance, increasing uptime and reducing maintenance costs. The three main features for innovative decanter technology, resulting in effective management of time and money, are as follows:
• Remote support and monitoring, enabling product and process experts to remotely monitor current or historical operational parameters and support plant staff on mechanical troubleshooting and/or process optimisation. Authorised customer staff are also allowed to monitor remotely when they are not present at the plant. Alarms and notifications can be sent out to relevant people and the next service activity could also be specified beforehand. This benefits customers around the world with time efficiencies and money saving.
• Maintenance support systems can monitor the vibration values of the bearings to detect extraordinary levels, and create an early incident report via a specifically developed algorithm. This report could include corrective actions to prevent a possible severe failure of the bearing(s). With the data monitored 24/7 and stored, even the remaining lifetime of the bearing can be precisely predicted. Again, this results in significant time and money savings.
• Constant solids loading and adaptive polymer control is a process optimization system helping customers to continue dosing the right amount of polymer during the entire sludge treatment operation with the decanter. There are two options to this process. Either by fixing the solids loading and poly flow and adjusting the feed flow, or by fixing the feed flow and adjusting the poly flow. Both are based on the feed sludge inlet with the concentration monitored continuously. Over or under dosing polymer is an unnoticeable cost element where adjustments have to be made manually but when such a feature is present and working, customers can have the peace of mind that their polymer dosage consumption is under control.
From the above, it is obvious that automation for decanters is an on-going journey and it is great to see some companies resourcing their innovations and launching new features. Customers are benefitting from efficient usage of time and money, with the environment kept clean fwor future generations. The advancement of automation technology will enhance the capabilities of business to provide more uptime and drive growth.