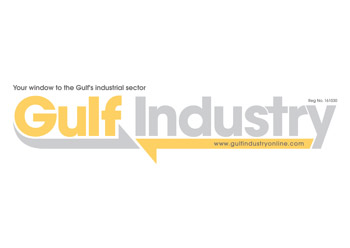

An innovative flat die design originally developed to stop melt leakage at the deckled portions of the die gap in extrusion coating now provides the same benefits for cast film, according to Extrusion Dies, Inc. (EDI).
Leakage has been a persistent problem with deckles, which are movable barriers at both ends of the die that enable operators to change product width for each job run. EDI's new system combines an internal deckle (which blocks flow with blades between the die lips) and an external deckle (which seals off the die gap from outside).
"Because the external deckle is linked to the drive of the internal deckle, the units function as one system, providing precisely coordinated movement and a truly leak-proof barrier," said Sam G. Iuliano, manager of technical sales.
External deckles provide more effective seals than internal deckles, whose main advantage is their more streamlined diversion of melt flow. While the external deckle in the coating version of EDI's new system covers both die lips, for the film version EDI has developed one that mounts only on the flexible-lip side of the slit, leaving the fixed-lip side unobstructed to ensure that the air gap necessary between lips and casting roll is not compromised.
"The streamlining achievable with an internal deckle is even more important for cast film than for coatings, which are more `forgiving' of hang-ups or dead spots in melt flow," said Iuliano. "In cast film, the polymer degradation caused by such flow disruptions can cause serious optical defects and degrade physical properties."
"Even though the melt pressure behind a deckle can be very high, a well-designed deckle should be leak-proof if the operator fully tightens the lip-adjusting bolts at each product changeover," said Iuliano. "In the real world, however, operators often do not tighten the bolts fully, opting instead for a torque level that allows blade movement without need for loosening and retightening the bolts."
EDI provides the new dual-deckle system with a motorised drive or a manual one operated by means of a hand-wheel.
Extrusion Dies Inc is a leading international supplier of flat dies for sheet and film, coating and palletising, shipping more than 500 dies and coextrusion feedblocks per year. The company designs and manufactures dies, feedblocks, deckling systems, vacuum boxes and related equipment.
Its subsidiaries include EDI Europe, based in Wiehl-Hubender, Germany; and Extrusion Dies, UK, in Whetstone, Leicester, England.
In the US, Germany and the UK, EDI operates facilities dedicated to reworking its own dies and those built by other suppliers, and it has licensed another rework facility in Japan.
Headquartered in Chippewa Falls, Wisconsin, US, EDI sells half of its dies outside the US.