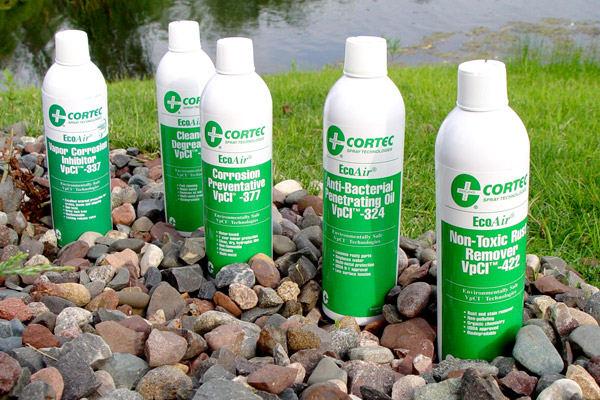
Corrosion specialist Cortec has advised industries setting up a rust removal station with Cortec VpCI-422, a USDA certified biobased product, to preserve machine parts that get rusted.
There are two types of companies that will typically benefit most from setting up a VpCI-422 rust removal station -- those that provide services to heavy industry (entire companies can be based on rust removal); and those that want to make better use of maintenance budgets by in-house chemical rust removal instead of more labour-intensive options, a Cortec release said.
Purposes for rust removal include everything from touching up the occasional rusty part that maintenance teams encounter around the plant, to reclaiming millions of dollars’ worth of inventory that has been sitting in poor storage conditions at an oil and gas facility. In each case, the underlying goal is to preserve the value of the component and extend its service life by restoring it to usable condition.
Rust removal setups
Rust removal setups range from simple to complex depending on the size of the components and the length of the job. For example, a one-time job to clean up a handful of rusty parts around the facility may only mean that maintenance needs three dishpans and a mesh steamer basket to dip and remove very small items such as nuts and bolts.
Another option for sporadic rust removal is to place the rust removal solutions in portable self-contained units that can be moved from one part of the plant to another without spilling concerns. If rust removal is a recurring activity, workers may want to install permanent tubs in a designated area. In some cases, tubs will need to be large enough to hold a giant gear or valve, and cranes may be needed to raise and lower the part. If desired, bubblers and heaters can be added to speed up the rust removal action of VpCI-422.
Identifying the stages of rust removal
Before setting up a VpCI-422 rust removal station, workers should identify how many stages of the process are needed. At minimum, there should be three: VpCI-422, rinsewater, and an alkaline cleaning fluid (e.g., VpCI-41x Series). However, workers should first ask if the parts are dirty or greasy, in which case a precleaning stage is needed to degrease and rinse the parts before dipping them in VpCI-422 (which removes rust but not dirt or grease). Following rust removal, a preservation step is often critical to preserve what was restored.
How to remove rust
Once the stations are set up, rust removal proceeds as follows:
*Clean and degrease the part if needed.
*Immerse the part in VpCI-422 for one hour to 24 hours depending on the severity of the rust. Workers may check the components periodically to see how rust removal is proceeding.
*Dip the parts in plain water to rinse away any residual VpCI-422 and corrosion products so as not to contaminate the final neutralising bath. At this stage, the worker can proceed to the final rinse or perform another round of rust removal.
*Dip satisfactory parts in an alkaline cleaner such as VpCI-414, which neutralises the acid and inhibits flash rust.
*Dry the parts and preserve them against further rusting in storage or transit. This step can take a variety of forms, including dipping the part into a bath of VpCI-377 or BioCorr water-based rust preventatives or simply enclosing the dry part in VpCI Film and Bags or other VpCI packaging materials.
Rust removal with VpCI-422 can make a major difference in a firm’s inventory value. By understanding the steps and equipment involved, companies can save asset value with a very simple process, the release added.--TradeArabia News Service